The Complete Guide to Boosting Workplace Productivity in Non-Desk Industries
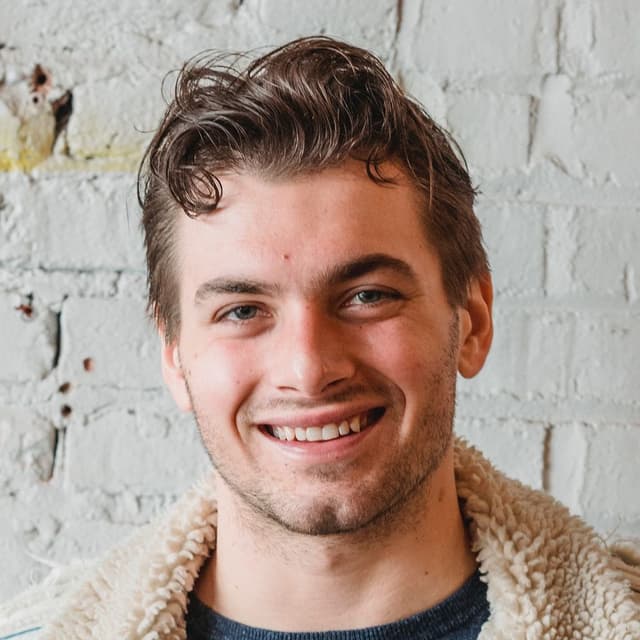
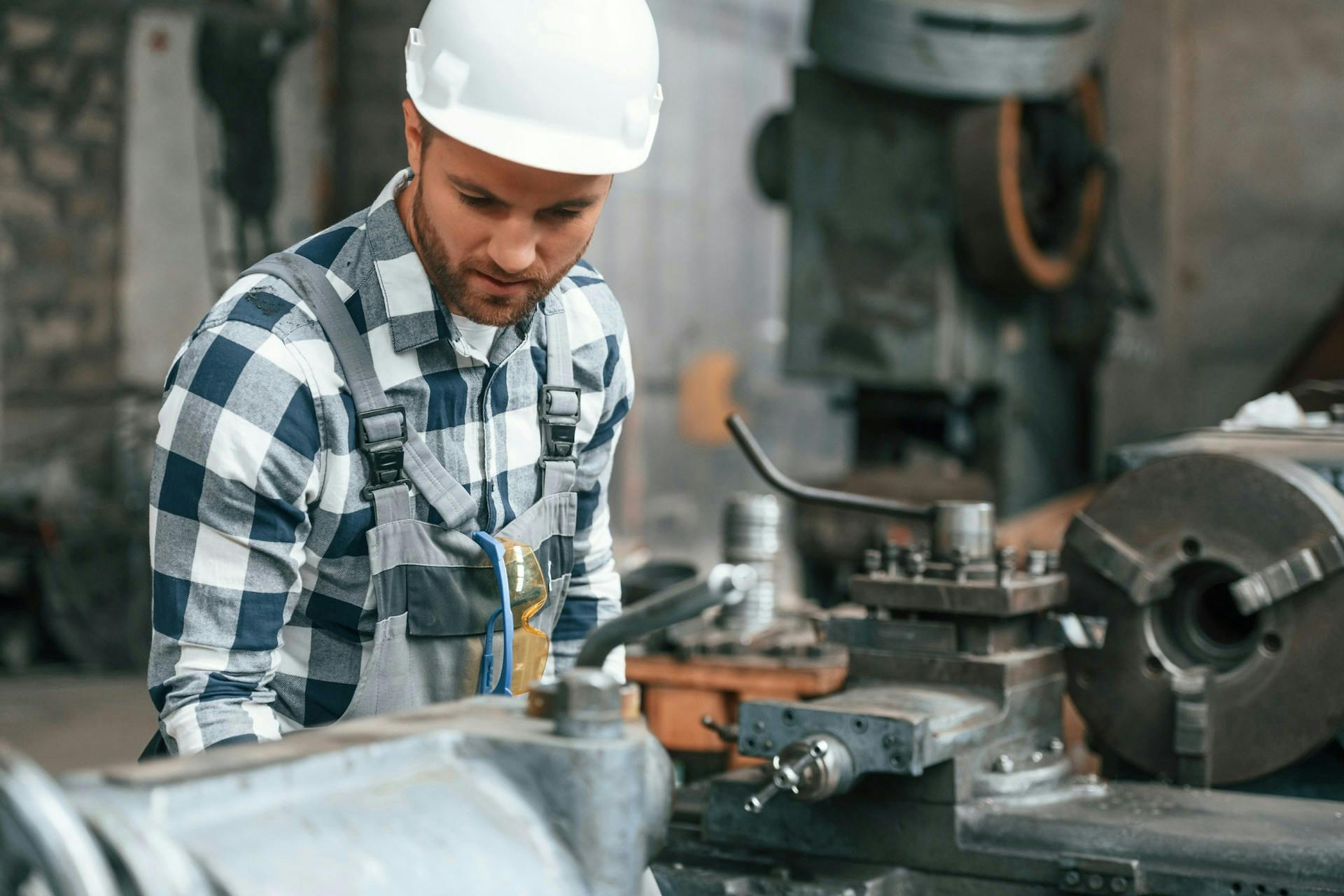
Many workplaces equate busyness with productivity, but true efficiency comes from meaningful work that delivers real results. Cal Newport's concept of "deep work" emphasizes distraction-free concentration that pushes cognitive limits, leading to high-quality, hard-to-replicate outcomes.
In contrast, "shallow work" consists of routine tasks often done with distractions. When employees engage in deep work, they enter a state of "flow," where focused immersion boosts productivity and job satisfaction.
Defining True Workplace Productivity
The traditional productivity formula—output divided by input—emphasized quantity alone, failing to capture what matters in modern workplaces. Today's manufacturing and industrial environments demand a refined approach where productivity means achieving meaningful, high-quality results efficiently.
Modern Approaches to Workplace Productivity
The traditional workplace tied productivity to physical presence—a leftover from industrial-era thinking. Manufacturing and industrial environments now recognize that productivity happens where conditions support workers' best efforts, not merely where their bodies happen to be.
Modern workplace productivity balances output (the results produced), input (resources used), and quality (value created), which together help to improve manufacturing productivity. This balanced view helps HR professionals in manufacturing environments focus on enabling effective work rather than simply monitoring hours clocked.
Breaking the connection between physical presence and productivity allows for smarter workforce management, especially important when supervising employees across multiple shifts, locations, or when introducing flexible scheduling options now making their way into traditionally rigid work environments.
Engagement and Purpose in Workplace Productivity
Gallup research found that highly engaged teams are 17% more productive and deliver 23% higher profitability. Workplace productivity transcends task completion; it represents value creation.
For manufacturing environments, this means workers who understand the purpose behind assembly procedures are more likely to identify improvement opportunities and maintain higher quality standards.
McKinsey research shows that 70% of employees believe their sense of purpose connects to their work, directly driving performance. Yet only 13% of employees worldwide report being fully engaged—representing an enormous opportunity for manufacturing HR teams to enhance employee engagement.
Organizations recognizing true workplace productivity set clear metrics focused on outcomes, not hours worked or tasks completed. This creates environments where factory floor workers and warehouse staff perform high-value work instead of busywork.
Incentive compensation strategies further motivate them, resulting in better production quality, fewer errors, and more meaningful contributions across the entire operation.
The Deep Work Concept and Workplace Productivity
Manufacturing and industrial workplaces face unique challenges in productivity with constant pressure to maintain output while managing workforce constraints. Deep work principles offer valuable solutions for these environments, helping workers focus on what truly matters.
Defining Deep Work in the Context of Workplace Productivity
Deep work is "professional activity performed in a state of distraction-free concentration that pushes your cognitive capabilities to their limit. These efforts create new value, improve your skill, and are hard to replicate." Cal Newport introduced this concept in his 2012 book Deep Work: Rules for Focused Success in a Distracted World.
For manufacturing workers, deep work happens during focused equipment maintenance, quality control inspections, or process improvement analysis. The opposite—shallow work—occurs when employees move through motions without concentration, like filling out routine paperwork while distracted or monitoring equipment without proper attention.
Both work types matter in manufacturing settings, but deep work doesn't happen accidentally. It requires intention. Line workers and warehouse staff face constant distractions from equipment alarms, intercom announcements, task switching, managerial check-ins, coworker conversations, and physical disruptions like aisle blockages or spills.
Even in seemingly routine manufacturing environments, creating opportunities for employees to focus completely on specific tasks improves quality outcomes and reduces errors.
Production supervisors who understand this distinction can structure workflows to prioritize concentrated effort during complex procedures while grouping simpler tasks during predictable energy lulls throughout shifts.
The Benefits of Deep Work in Enhancing Workplace Productivity
When factory, warehouse, or logistics employees engage in deep work, they experience substantial advantages: higher productivity, enhanced safety awareness, and greater engagement with their responsibilities.
During successful deep work sessions, production workers often enter a "flow" state—becoming fully immersed in the task, whether troubleshooting equipment issues or executing precision quality checks. This focused state improves manufacturing outcomes and personal satisfaction.
Consider how Toyota implemented focused problem-solving sessions where maintenance teams disconnect from routine interruptions to analyze persistent equipment issues. These dedicated periods resulted in solutions that automated monitoring systems alone couldn't identify.
Deep work matters in industrial settings because it elevates employees beyond mechanical task completion to active problem-solving and continuous improvement. Manufacturing workers report greater job satisfaction when they have opportunities to concentrate fully on meaningful aspects of production.
Research on employee engagement demonstrates that when production staff feel competent and recognized for substantive contributions, they develop greater ownership over quality and efficiency outcomes.
Without deep work opportunities, manufacturing employees remain trapped in repetitive motions, never reaching their potential to improve systems or processes.
Identifying and Addressing Workplace Productivity Killers
Understanding what hinders productivity in manufacturing and industrial environments helps HR professionals target improvement efforts effectively. Once these obstacles become clear, solutions can follow.
Common Workplace Productivity Killers
Several recurring issues undermine manufacturing efficiency:
- Frequent and inefficient meetings: Shift handover meetings and production briefings become productivity barriers when they run too long or include unnecessary personnel. These pull manufacturing workers away from production lines and disrupt work rhythms.
- Lack of standardization: Manufacturing employees waste valuable time figuring out how to complete tasks without clear processes. This creates inconsistency—either over-processing (excessive steps) or under-processing (skipping important quality checks), and may lead to compliance issues.
- Ineffective communication: When manufacturing workers lack clarity about production priorities, they spend time hunting for answers instead of focusing on output. This confusion frustrates line workers and degrades factory floor culture.
- Technology distractions: While technology enhances production monitoring, constant alerts and notifications fragment attention and make focused maintenance or quality work nearly impossible for industrial employees.
Strategies to Combat These Challenges
Here are practical approaches manufacturing HR teams can implement to address productivity obstacles:
- Rethink production meetings: Brief line workers on agendas beforehand. Assign someone to keep discussions focused on production issues. Keep shift meetings concise with specific purposes. Question whether each meeting serves an actual production need or if information could be shared through other methods.
- Standardize manufacturing processes: Document production workflows with clear steps. This reduces decision fatigue among line workers, creates consistency in output, and improves training for new manufacturing employees.
- Improve factory communication channels: Manufacturing companies with effective communication are 50% more likely to have lower employee turnover. Ensure floor supervisors provide consistent guidance about production priorities and establish regular, scheduled check-ins with line workers. Make sure that they are not unannounced check-ins as this can disrupt flow. Create information sharing between departments through daily production boards or cross-functional manufacturing teams.
- Establish technology boundaries: Create guidelines for responding to production alerts. Designate focus periods when interruptions are minimized for maintenance tasks. Encourage "notification-free" blocks for quality inspection or equipment setup.
- Build two-way communication: Manufacturing environments benefit from channels where line workers can communicate upward about production issues. This identifies problems early, builds loyalty among factory workers, and improves decision-making about process improvements.
Designing Workspaces for Deep Work and Workplace Productivity
The physical environments where manufacturing and warehouse employees work significantly impact their ability to focus and handle complex tasks, directly influencing production output and quality.
Physical and Virtual Workspace Design for Optimal Workplace Productivity
Manufacturing environments should minimize distractions and maximize focus opportunities. Traditional factory layouts don't always accommodate concentrated tasks; instead, consider adaptable manufacturing spaces suited for focused work alongside production areas.
While manufacturing requires collaborative zones for team interactions, deep work necessitates designated areas where maintenance technicians or quality specialists can retreat for complex problem-solving. These spaces should indicate to others that interruptions should be minimal during troubleshooting or analysis work.
Natural environment elements can meaningfully enhance industrial workspaces. Proper lighting, noise reduction, and designated quiet zones reduce stress, improve mood, and boost cognitive function among production workers. These aren't merely decorative—they actively support mental capacity for sustained focus on manufacturing tasks.
For effective deep work in manufacturing settings, establish consistent, quiet environments with necessary resources readily available. Production supervisors might consider scheduling specific uninterrupted time blocks for maintenance teams or quality specialists to work on complex issues without constant interruptions from routine production matters.
Manufacturing workers perform better when they can count on dedicated focus time for their most challenging responsibilities rather than constantly switching between tasks of varying complexity throughout their shifts.
The Role of Technology and Digital Workspaces in Workplace Productivity
Digital tools in manufacturing require thoughtful implementation to support concentration rather than disrupt it.
Production management platforms like manufacturing execution systems can organize workflow and maintain visibility while minimizing unnecessary interruptions. Configure these tools to send alerts only for truly urgent production issues during focused maintenance or quality assurance sessions.
When designing digital systems for manufacturing environments, emphasize simplicity. Remove unnecessary steps in data entry, limit non-essential notifications, and create interfaces that enable concentration rather than constant distraction.
Yourco is an SMS-based communication platform that plays a crucial role in supporting focused work by streamlining employee communication without adding digital clutter. Unlike traditional workplace apps that require downloads and frequent logins, Yourco’s SMS-based platform ensures essential updates reach workers without unnecessary distractions. HR and operations managers can use Yourco’s segmentation and automation features to deliver only the most relevant messages, allowing production teams to stay informed while maintaining deep focus.
Even well-designed manufacturing workspaces require personal and organizational discipline. Production managers who consistently protect time for focused work on their teams strengthen this capability over time. This leads to better manufacturing outcomes, innovative process improvements, and greater work satisfaction among industrial employees who appreciate the chance to apply their expertise without constant interruption.
Practical Implementation of Deep Work Principles for Workplace Productivity
As an HR or operations manager in manufacturing, you can promote focused work through several approaches:
- Develop organization-wide focused work policies: Establish guidelines that protect concentrated work time for maintenance teams, such as interruption-free troubleshooting periods or designated quiet zones on the production floor.
- Configure industrial workspaces thoughtfully: Arrange manufacturing areas to minimize unnecessary distractions and provide quiet spaces specifically for complex analysis or detailed quality inspections.
- Structure team focus routines: Help production teams block specific time periods for uninterrupted concentration on complex tasks. Consider structured approaches like the Pomodoro method adapted for manufacturing environments.
- Establish interruption protocols: Develop clear communication guidelines about when maintenance or quality teams are in focused work mode and how to respect those boundaries. This might include visual indicators in work areas or shared production schedules showing when teams should not be interrupted except for true emergencies.
- Track and highlight focused work results: Develop metrics that value quality outcomes rather than mere activity, and recognize team members who demonstrate effective focused work practices that improve production or maintenance results.
- Ensure employees can provide feedback or suggestions: Encouraging employees to share feedback on workplace distractions is essential for improving productivity. When workers can voice their challenges and suggest solutions, businesses can identify hidden inefficiencies, reduce interruptions, and create a more focused work environment. With Yourco’s SMS-based polling and surveys, employees can easily provide real-time input without disrupting their workflow. Acting on their insights fosters engagement, boosts morale, and ultimately enhances operational efficiency.
Connecting with Your Non-Desk Workforce for Improved Workplace Productivity
Manufacturing and industrial non-desk workers benefit most from a multichannel communication approach designed for their specific work environments. Without regular email or computer access, they rely on timely updates to perform effectively.
Consequently, SMS-based communication has emerged as the primary method for communicating with non-desk workers. While SMS-based communication remains the preferred method, you can also use other channels to enhance your communication strategy into a multichannel approach. Consider using:
- Digital information boards throughout production facilities for important announcements
- Video messages from management for significant safety or production updates
- Voice response systems for accessing scheduling information
Manufacturing communication should flow bidirectionally. Use regular brief employee surveys to gather real-time insights about production floor employee engagement and work experiences.
When actively seeking and applying feedback, you demonstrate that you value non-desk employees' perspectives, which significantly reduces employee turnover and improves workplace productivity across manufacturing operations.
Maximize Your Workforce's Full Potential for Workplace Productivity
Implementing focused work principles transforms productivity in manufacturing environments. The challenge of connecting with production workers requires solutions beyond traditional communication methods.
Yourco offers an SMS-based platform specifically for non-desk workers that requires no app downloads or technical training. Manufacturing employees use their existing phones and texting abilities to receive announcements, provide feedback through simple surveys, and maintain communication regardless of their location.
Try Yourco for free today or schedule a demo and see the difference the right workplace communication solution can make in your company.