Step-by-Step Guide to Standard Operating Procedure Format
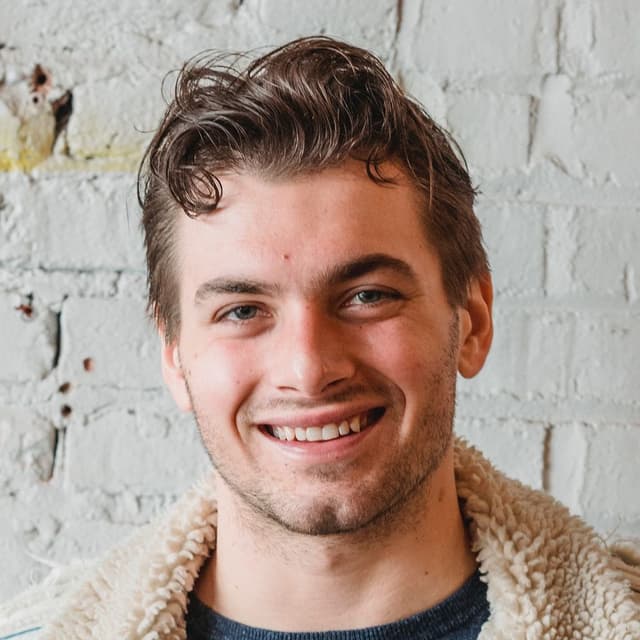
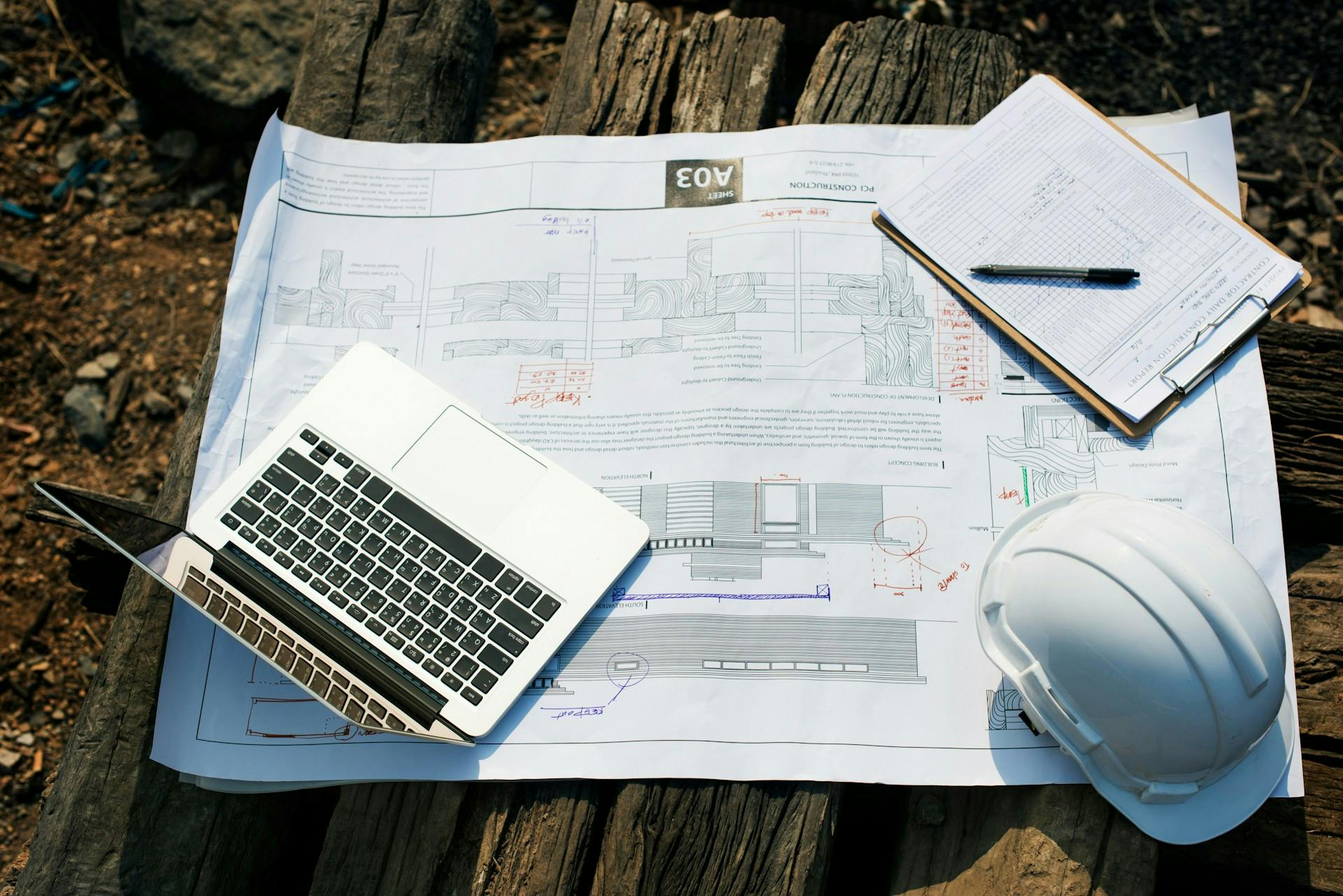
Standard Operating Procedures (SOPs) are documented, step-by-step instructions that outline how to perform routine operations within your organization. Selecting an appropriate standard operating procedure format matters because they establish operational consistency, quality control, and regulatory compliance—especially important for frontline workers in changing environments.
Well-implemented SOPs reduce variability in task performance, directly impacting your bottom line and operational effectiveness.
For non-desk employees who face challenges like limited computer access, varying literacy levels, noisy surroundings, and the need to reference information while working, the right format makes the difference between procedures that get followed and those that don't.
The Foundation of an Effective Standard Operating Procedure Format
Every successful Standard Operating Procedure (SOP) shares common components regardless of its format. These elements ensure both SOP compliance and practical usability:
- Purpose statement: Defines why the SOP exists and what it aims to accomplish
- Scope: Outlines which activities, departments, or situations the SOP covers
- Roles and responsibilities: Identifies who performs each task and who's accountable
- Equipment and materials: Lists all tools, supplies, or systems needed
- Step-by-step procedures: Details the exact sequence of actions to follow
- Quality controls: Establishes checkpoints and standards to ensure proper execution
- Exception handling: Provides guidance for unexpected situations or deviations
- Revision history: Tracks changes and ensures everyone uses the most current version
These components form the backbone of any effective standard operating procedure format, whether it's a simple checklist, detailed flowchart, or visual guide. Before choosing a format, make sure you've addressed these elements to build SOPs that truly serve your team's needs.
SOP Format Types: Choosing the Right Standard Operating Procedure Format
When creating standard operating procedures for non-desk employees, selecting the right standard operating procedure format is necessary for ensuring comprehension, usability, and compliance. Different format types serve various purposes and work environments, so understanding their strengths and limitations will help you create more effective SOPs.
Step-by-Step and Hierarchical Standard Operating Procedure Formats
Step-by-step formats present instructions in a linear, numbered sequence, making them ideal for straightforward, routine procedures. This format works exceptionally well for non-desk employees because it:
- Provides clear progression of tasks
- Minimizes errors through explicit instructions
- Is easy to follow, even in fast-paced environments
For example, a simple step-by-step SOP for operating a forklift might include:
- Conduct pre-operation inspection
- Mount the forklift using 3-point contact
- Fasten seatbelt
- Start the engine
- Test controls
However, for more complex procedures, a hierarchical standard operating procedure format offers advantages by breaking down processes into main steps and substeps. This provides both overview and detailed guidance, allowing workers to quickly reference main steps while having access to more specific instructions when needed.
A hierarchical SOP for cleaning a hotel room might look like:
- Prepare cleaning cart
1.1 Stock linens
1.2 Restock cleaning supplies
1.3 Check equipment functionality - Enter room
2.1 Knock and announce presence
2.2 Open curtains and windows
2.3 Remove trash
The main disadvantage of these formats for non-desk workers is that hierarchical structures can become visually overwhelming in high-pressure situations, while simple step-by-step formats might oversimplify complex tasks.
Flowchart Standard Operating Procedure Format
Flowcharts are particularly effective for procedures that include decision points or multiple possible paths. For non-desk employees who need to make quick decisions based on changing variables, flowcharts provide:
- Visual representation of the entire process
- Clear indication of decision points and alternative paths
- Easy-to-follow structure for complex procedures
Essential flowchart elements include start/end points, process steps (rectangles), decision points (diamonds), and directional arrows showing the flow of activities. This format works well for procedures like handling customer complaints or troubleshooting equipment issues.
The primary challenge of flowcharts for non-desk workers is that they can be difficult to follow on small screens or in certain environmental conditions. They also require some familiarity with flowchart symbols to be effective.
Checklist Standard Operating Procedure Format
Checklists are ideal for verification procedures, routine maintenance, and tasks requiring confirmation of completion. They provide non-desk employees with:
- Simple, intuitive structure
- Clear sense of progress as items are checked off
- Quick confirmation that all steps have been completed
For example, a restaurant opening checklist might include:
- Unlock front and back doors
- Turn on lights
- Check walk-in cooler temperatures
- Start ovens and grills
- Brew coffee
- Set up cash registers
Checklists are excellent for non-desk workers performing repetitive tasks or safety-critical procedures. However, they typically lack explanatory detail, making them less suitable as standalone SOPs for complex or technical procedures that require deeper understanding.
Visual and Hybrid Standard Operating Procedure Formats
Visual-heavy formats use images, diagrams, or infographics to illustrate procedures, which is particularly effective for non-desk employees who:
- Are visual learners
- May face language barriers
- Need to understand spatial relationships or physical movements
- Work in diverse, multilingual environments
For instance, a visual SOP for proper handwashing in food service might show a series of images demonstrating each step of the process, from wetting hands to turning off the faucet with a paper towel.
Hybrid formats combine multiple approaches for comprehensive coverage. You might create a procedure that uses:
- A flowchart for the overall process
- Step-by-step instructions for complex parts
- Visual elements to demonstrate physical tasks
- A final checklist for verification
This approach provides the benefits of multiple formats while minimizing their individual limitations. For non-desk workers who may need different levels of detail depending on their experience or the specific situation, hybrid formats offer the flexibility to quickly find the appropriate guidance.
When choosing a standard operating procedure format for non-desk employees, consider the work environment (noise, lighting, space constraints), the complexity of the tasks, and the characteristics of your workforce (language skills, experience level).
Often, the most effective approach is to combine formats to create comprehensive SOPs that accommodate different learning styles and information needs.
Industry-Specific Standard Operating Procedure Formats
Different industries face unique challenges and operational requirements that necessitate specialized standard operating procedure formats. Adapting standard formats to industry-specific needs helps organizations improve procedure adoption, compliance, and overall effectiveness.
Manufacturing Standard Operating Procedure Formats
In manufacturing environments, SOPs must address machine operation, quality control, and safety protocols while considering the fast-paced nature of production floors.
Manufacturing facilities benefit greatly from visual-centric SOPs that minimize text and maximize graphical elements. This approach is particularly effective because:
- Assembly line workers often need to reference procedures quickly
- Noisy environments can make verbal communication challenging
- Safety information, including essential safety rules, must be immediately recognizable
Effective manufacturing SOPs typically include:
- Color-coded safety warnings
- Exploded-view diagrams of machinery
- Visual quality control checkpoints
- Sequential photographs of correct assembly procedures
- Clear troubleshooting decision trees
Facility Management Services Formats
Facility management settings require SOPs that address strict regulatory compliance, cleaning protocols, and safety standards. These procedures must be meticulously designed to prevent errors that could have serious consequences.
In facility management environments, SOPs need to:
- Comply with OSHA, EPA, and other regulatory standards
- Address various specialized roles (custodians, maintenance technicians, security personnel)
- Provide clear guidance for emergency situations
- Include thorough documentation requirements
One successful example comes from a facility services company that revised their cleaning SOPs from text-heavy documents to a combination of checklists and visual guides. This change resulted in an improvement in cleaning thoroughness and a significant reduction in workplace accidents.
Facility management SOPs frequently employ hierarchical standard operating procedure formats with clear role designations. For cleaning procedures specifically, effective SOPs typically include:
- Step-by-step checklists for equipment operation
- Photographic demonstrations of proper cleaning techniques
- Emergency response flowcharts
- Clear documentation requirements
- Decision matrices for handling different types of waste materials
Field Service Standard Operating Procedure Formats
Field service personnel face unique challenges as they work in varied, often unpredictable environments away from central offices. Their SOPs must be accessible, concise, and usable in diverse conditions, often including overcoming language barriers.
For field service workers, the most effective SOPs are:
- Accessible offline
- Heavily visual with minimal text
- Searchable by task or equipment type
- Modular and focused on specific tasks
A successful approach to field service SOPs is implementing SMS-based solutions that provide workers with access to procedures, safety checklists, and real-time updates on site conditions. Construction companies, utility providers, and telecom services have all benefited from this approach.
Field service SOPs typically emphasize:
- Weather-related contingency procedures
- Equipment troubleshooting guides with photographs
- Customer interaction protocols
- Safety checklists for various environments
- GPS-linked site-specific information
- QR codes on equipment linking to relevant operating instructions
Tailoring standard operating procedure formats to these industry-specific requirements helps organizations improve procedure compliance, reduce errors, and enhance overall operational efficiency.
The most successful implementations combine traditional documentation approaches with modern technological solutions that meet the unique needs of each work environment.
Visual Communication Techniques for Non-Desk Employees
When your workforce doesn't sit at desks or computers all day, text-heavy SOPs won't work. Visual communication techniques ensure your frontline workers can quickly understand and correctly follow procedures. Let's explore some visual approaches that can turn your SOPs into accessible, easy-to-follow guides.
Icons, Color-Coding, and Visual Cues
Visual elements aren't decorative extras—they're powerful communication tools that dramatically improve how well your team understands and remembers SOPs:
- Icons and symbols: Use recognizable symbols for actions, tools, or concepts. Icons create an intuitive visual language that helps employees quickly spot important information without reading text. Pick universally recognized symbols and use them consistently across all your documentation.
- Color-coding: Use strategic color systems to categorize information, highlight important steps, or show safety levels. When creating your color system:
- Use the same colors across all SOPs
- Stick to 4-5 core colors to avoid confusion
- Make sure your colors work for color-blind individuals
- Combine colors with patterns or textures for better distinction
- Visual hierarchies: Create clear visual pathways that guide the eye through the proper sequence of steps. Use numbered steps, arrows, or size differences to show importance.
- Step-by-step diagrams: Break complex procedures into clear, sequential visuals showing exactly what happens at each stage. This works especially well for assembly processes, cleaning procedures, or equipment operation.
Creating Visuals That Transcend Language Barriers
Your SOPs may need to be understood by employees speaking different languages or with varying literacy levels. Visual communication offers a powerful solution for communicating with non-English speaking employees:
- Universal design principles: Create intuitive visual guides that need minimal text to understand. Use arrows, sequencing, and clear imagery that communicates regardless of language ability.
- Real photographs: Include actual photos of equipment, workspaces, or employees performing tasks correctly. This provides concrete, contextual understanding that words might miss.
- Before and after images: Show both incorrect and correct ways to perform tasks, clearly marking which is which through visual cues like check marks or X marks.
- Visual warnings: Create clear visual indicators for safety hazards, required protective equipment, or quality checkpoints using high-contrast colors and internationally recognized symbols.
- Video demonstrations: For complex procedures, add short video demonstrations accessible via QR codes placed directly on equipment or workstations.
For text in your visual SOPs, use sans-serif fonts at a minimum size of 16 pixels or 12 points. Create a clear hierarchy with distinct headings and subheadings, and leave enough white space to prevent visual overload.
When designing visual SOPs, remember the goal isn't making your procedures prettier—it's improving comprehension, reducing errors, and creating a safer, more efficient workplace.
Through thoughtful implementation of icons, color-coding, and visual hierarchies that work across language barriers, you'll create SOPs your non-desk employees can actually use and understand in their daily work.
Physical Format Considerations for Work Environments
When implementing SOPs for non-desk employees, the physical presentation of these procedures can significantly impact their effectiveness. Unlike office workers who may primarily access digital documents, frontline workers often need physical formats that are accessible in their specific work environments.
Laminated cards or sheets offer durability and protection against moisture, dirt, and wear—making them ideal for manufacturing floors, kitchens, or outdoor work sites. These can be hole-punched and attached to equipment or kept in accessible locations for quick reference.
Binders organized by department or process type provide a comprehensive solution when multiple SOPs need to be accessible in one location. These work well in control rooms, nurse stations, or maintenance areas where employees may need to consult various procedures.
Wall-mounted posters are highly effective for frequently used procedures or safety protocols. Consider placing these:
- Directly at workstations where procedures are performed
- In high-visibility common areas
- Near relevant equipment or machinery
- At entry and exit points for safety procedures
Color-coding can enhance the usability of physical SOPs, helping employees quickly identify different types of procedures (safety protocols in red, quality procedures in blue, etc.). This visual distinction is particularly valuable in fast-paced environments where time is limited.
For harsh environments, consider specialized materials like waterproof paper, metal-backed instructions, or plastic-encased documents that can withstand extreme temperatures, chemicals, or outdoor conditions.
The best practice is to place physical SOPs exactly where they'll be needed, ensuring they remain visible, accessible, and protected from the specific conditions of your work environment.
Digital Solutions for Field Access
When your team works primarily in the field—on factory floors, construction sites, or service locations—paper-based SOPs just don't cut it. Digital solutions designed specifically for reaching non-desk employees dramatically improve both accessibility and compliance.
Mobile Responsiveness and Intuitive Design
SMS-based platforms have become essential tools for communication tools for deskless workers, making SMS-optimized SOPs a necessity. When designing SOPs for SMS access, focus on:
- Creating concise content with simple, clear instructions
- Using numbered steps that are easy to follow via text
- Breaking complex procedures into multiple messages in a logical sequence
- Ensuring important information appears first in every message
SMS-first design isn't just about shrinking content to fit a message; it’s about rethinking how information is structured and accessed. This involves prioritizing the most important information and eliminating unnecessary details, ensuring that employees can easily follow steps and understand essential tasks in real time.
QR Codes and Offline Capabilities
QR codes create a seamless bridge between physical work environments and digital information. You can implement QR solutions by:
- Placing QR codes on equipment linking directly to operation and maintenance SOPs
- Adding QR stickers in workspaces that connect to relevant safety procedures
- Creating QR-based troubleshooting guides for common issues
- Using QR codes in training materials to provide access to resources
For these solutions to work in real-world environments, offline capabilities are necessary. Many industrial facilities, remote work sites, and field service locations have spotty network connectivity. Effective digital SOP platforms should:
- Work with basic SMS functionality that doesn't require data connections
- Provide important information even in low-connectivity areas
- Offer simplified versions of procedures via text message
- Function reliably in areas with limited network coverage
Interactive Digital Standard Operating Procedure Formats
Static PDFs rarely meet the needs of non-desk employees. Instead, develop truly interactive SOPs that take advantage of digital capabilities:
- Text message response options for completing procedure steps
- SMS-based verification for safety procedures
- Photo submission via text to document completion
- Step-by-step instructions delivered via scheduled text messages
- Decision-based responses that guide workers through complex procedures
For organizations operating in multiple locations, SMS-based platforms can significantly enhance multi-location efficiency by providing consistent SOPs across all sites.
These digital solutions transform your SOPs from static documents into dynamic, accessible tools that support your non-desk employees where and when they need guidance most. The focus should be understanding the specific challenges of your field environment and selecting technologies that address those unique needs.
That’s where Yourco makes a measurable difference. Purpose-built for reaching non-desk teams, Yourco delivers SOPs and procedure updates via SMS—no apps, no data plans, just instant, reliable access on any mobile phone. Workers can receive step by step instructions via text or even open linked SOP documents directly from text messages—all without needing to log in to complex systems or access a mobile app. Whether it’s sending scheduled step-by-step instructions, confirming safety protocol adherence through response-based workflows, or distributing site-specific SOPs across multiple locations, Yourco ensures your teams stay informed and compliant in real time. With built-in multilingual support and offline functionality, Yourco adapts to the realities of fieldwork, ensuring your procedures aren’t just documented, they’re followed.
Writing Standard Operating Procedure Formats for Maximum Comprehension
Creating SOPs that everyone can understand, regardless of educational background or reading level, is essential for ensuring consistent implementation. Clear communication helps improve team communication, making it more likely that your team will follow procedures correctly and consistently.
Simplify Your Language
Avoid jargon, technical terms, and complex sentence structures whenever possible. If you must use specialized terminology, provide clear definitions.
Before: "Prior to initiation of the sanitation protocol, personnel must ensure the appropriate dissolution of the quaternary ammonium compound in accordance with manufacturer specifications."
After: "Before cleaning, mix the cleaning solution according to the label instructions."
Use Active Voice
Active voice makes instructions clearer and easier to follow. In active voice, the subject of the sentence performs the action—this creates direct, task-focused guidance. Passive voice often leads to confusion about who is responsible for the task. In high-risk environments, using active voice helps eliminate ambiguity, increases accountability, and improves safety by making it clear who needs to do what—and when.
Before: “Protective gear must be worn before entering the site.”
After: “Wear your protective gear before entering the site.”
This small shift creates clarity. The second version tells the worker exactly what to do, without room for interpretation. It enhances understanding, improves compliance, and helps prevent critical safety oversights in environments where clear direction matters most.
Consider Reading Level
Aim for a reading level between 6th and 8th grade for maximum accessibility. This doesn't mean "dumbing down" your content—it means communicating clearly so that every employee, regardless of literacy level, can easily follow the instructions.
Using simple language and structure ensures that important information is accessible to everyone in your workforce. This clarity reduces confusion, improves task compliance, and enhances workplace safety.
Before: "In the event of an equipment malfunction, initiate the troubleshooting sequence and document all observations in the maintenance log prior to escalating to supervisory personnel."
After: "If equipment breaks down:
- Try the steps in the troubleshooting guide
- Write what happened in the maintenance log
- Tell your supervisor"
Reduce Cognitive Load
Break complex procedures into smaller, manageable steps. Use numbered lists for sequential tasks and bullet points for non-sequential items.
Before: "The workspace must be organized with all tools returned to their designated locations, debris removed from all surfaces, and floors swept and mopped at the conclusion of each shift, with particular attention to ensuring that safety equipment remains accessible and unobstructed."
After: "At the end of your shift:
- Put all tools back in their marked spots
- Clear all debris from surfaces
- Sweep and mop floors
- Make sure nothing blocks safety equipment"
Breaking the procedure down into smaller, actionable steps ensures workers know exactly what to do. It also reduces confusion, helps workers follow the process more effectively, and reinforces the importance of safety.
Choose the Right SOP Format with Yourco
Selecting an appropriate standard operating procedure format should be tailored to your organization's specific needs. Consider your workforce composition, task complexity, and industry requirements when making this decision. Implementing internal communication best practices is also important to ensure that SOPs are effectively communicated and adhered to by your workforce.
Yourco's SMS-based employee platform delivers SOPs directly to your non-desk workforce using text messaging—technology your employees already use daily. This ensures procedures are accessible even in environments with poor connectivity or when employees are constantly moving.
With Yourco, you can go beyond simple delivery. Schedule recurring SOP reminders, such as weekly toolbox topics, to reinforce high-risk activities like working at heights or handling hazardous materials. You can even help keep training top-of-mind by sending short SMS quizzes or knowledge checks that help reinforce retention and identify knowledge gaps in real time.
Yourco also supports instant SOP updates, allowing you to notify your entire team immediately when procedures change—critical for compliance-driven environments or fast-paced job sites. Everyone stays aligned, and you can be confident that the most up-to-date guidance is being followed across your operation.
Try Yourco for free today or schedule a demo and see the difference the right workplace communication solution can make in your company.