Creating Effective SOPs in Manufacturing: A Complete Guide with Tools & Templates
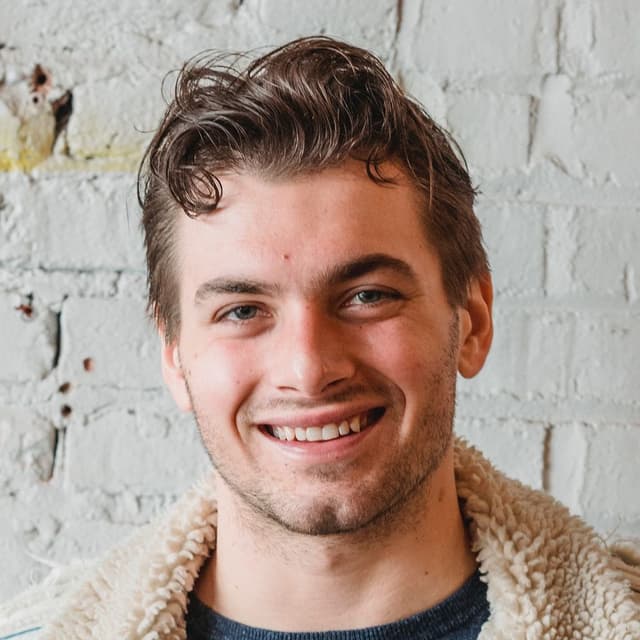
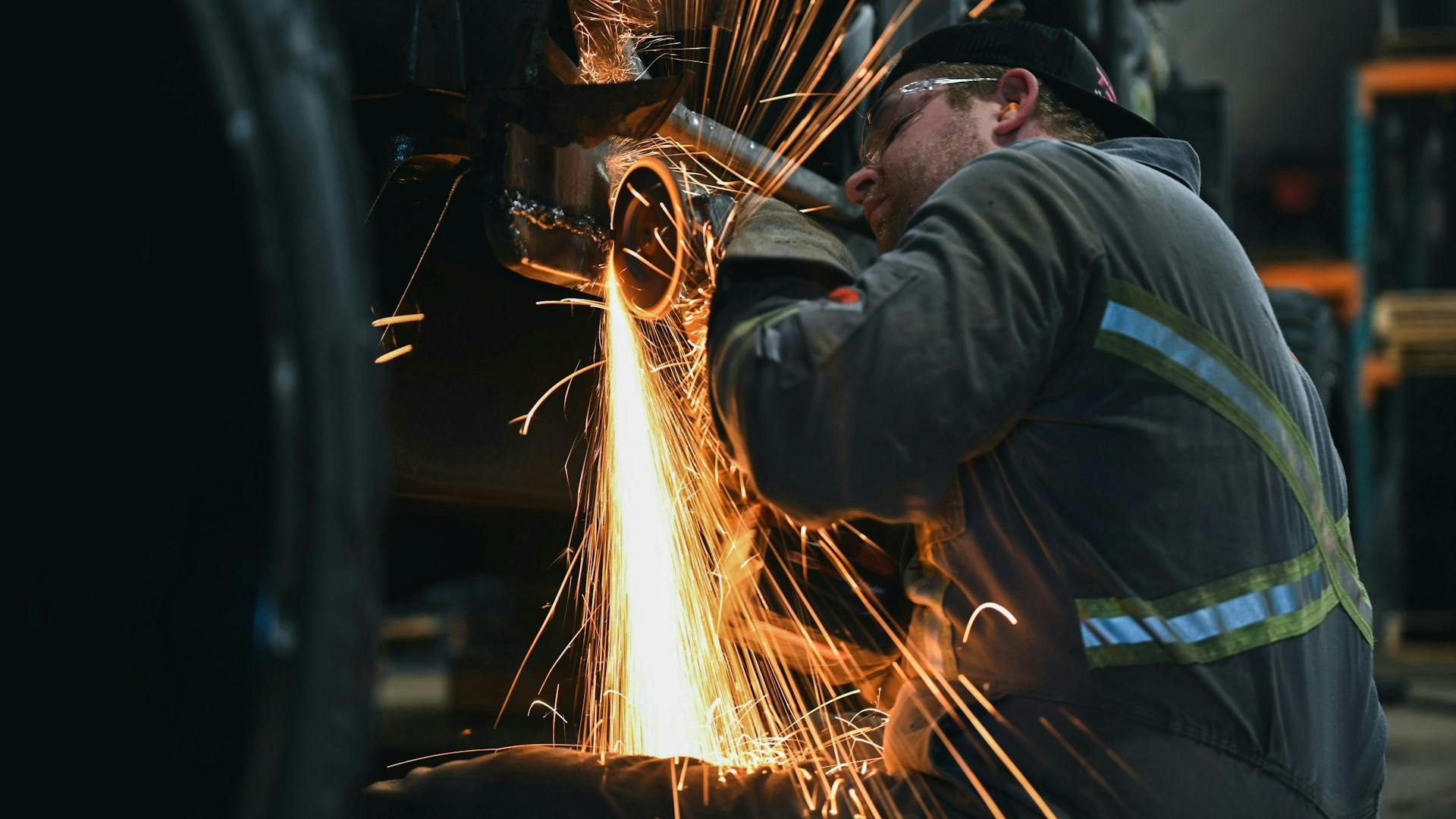
Standard Operating Procedures (SOPs) function as the backbone of manufacturing operations. These step-by-step instructions document protocols for specific tasks and processes, ensuring workers complete the same steps in the same way across shifts and locations.
SOPs play a fundamental role in the Plan-Do-Check-Act (PDCA) process used throughout manufacturing facilities. They form the planning phase where processes are documented before execution, verification, and improvement cycles begin. This approach aligns with global management standards like ISO 9001 that manufacturers follow for quality and consistency.
Well-developed SOPs minimize variations that cause defects, enhance quality control, ensure regulatory compliance, improve workplace safety, and contribute to operational excellence through improved communication and accountability.
What Are SOPs in the Manufacturing Industry?
Standard Operating Procedures (SOPs) in the manufacturing industry are comprehensive sets of step-by-step instructions designed to help team members perform tasks consistently.
As Chartered Engineer Giles Johnston puts it, SOPs are "the best agreed way of documenting the carrying out of a task." They're practical for complex tasks that must adhere to regulatory standards, ensuring efficiency and high-quality outputs.
SOPs are fundamental to a company's success because they ensure consistency and safety in organizational functions. When implemented effectively, SOPs reduce errors, increase operational efficiency, and enhance profitability while fostering a safer work environment.
Types of SOPs in Manufacturing Industry
SOPs in the manufacturing industry fall into two main categories based on their function and application. Technical SOPs focus on equipment operation, maintenance, and safety procedures, providing specific instructions for tasks requiring precision.
These include detailed steps for machine setup, troubleshooting protocols, and equipment maintenance schedules that help operators maintain consistent production standards.
Management SOPs address administrative processes like inventory management, quality assurance documentation, and production planning. These procedures establish frameworks for decision-making and operational oversight, ensuring departments work cohesively toward production goals.
Both types work together to create a comprehensive system that supports manufacturing operations from the shop floor to management offices.
Common Components of SOPs
Manufacturing SOPs contain several standard elements that make them effective tools for process control and worker guidance. They begin with clear objectives stating what the procedure accomplishes, followed by scope definitions outlining where and when the SOP applies.
Responsibility assignments identify which personnel handle specific tasks, while equipment and materials sections list everything needed to complete the procedure.
The heart of any SOP is the step-by-step instructions that explain exactly how to perform tasks, often accompanied by visual aids like photos or diagrams. Safety guidelines detail required protective equipment and hazard warnings, while troubleshooting sections address common problems operators might encounter.
Documentation requirements specify what records must be kept, including quality checks and completion verification. Together, these components create comprehensive guides that maintain consistency throughout manufacturing operations.
Methodology for Developing SOP in Manufacturing Industry
Developing effective SOPs in the manufacturing industry requires a systematic approach to ensure they're practical, comprehensive, and useful to your organization. Here's a step-by-step methodology to guide you through the process:
1. Conduct a Process Audit
Start by examining current workflows to identify processes needing standardization. Work with subject matter experts who perform these tasks daily to understand the actual steps involved, not just what management thinks should happen.
Document existing gaps where inconsistencies appear between shifts or between different operators performing the same task. Observe workers in action to capture nuances that might not appear in existing documentation. Track workflow patterns to identify bottlenecks or inefficient steps that could be improved.
Measure current performance metrics to establish a baseline for comparison after SOP implementation. Interview workers about challenges they face and workarounds they've developed.
This hands-on research uncovers the reality of your processes, allowing you to create SOPs that address actual working conditions rather than idealized versions of how things should work.
2. Define Scope and Objectives
Clearly define what your SOP will cover and what it aims to achieve. Specify exactly which equipment, processes, and situations the procedure applies to, and equally important, what falls outside its boundaries. Determine whether the SOP addresses a single task or a series of connected operations.
Establish measurable objectives that align with your production goals, quality standards, and safety requirements. Consider how the SOP supports broader departmental and organizational aims, such as reducing defect rates or improving production throughput. Identify which regulatory requirements the SOP must satisfy, including industry standards and internal compliance policies.
Determine who will use the SOP and what level of detail they require based on their expertise and training. Set specific performance indicators that will measure the SOP's effectiveness once implemented. This groundwork ensures your SOP serves a clear purpose and delivers measurable value to your operation.
3. Create Process Flow Maps
Process mapping visualizes each procedure step, showing exactly how tasks connect. Start by listing all activities in sequence, then add decision points where workers must make choices based on conditions. Include timing requirements for steps with waiting periods or duration limits.
Map material and information flows showing how products, paperwork, or data move through the process. Identify where quality checks occur and what standards apply at each point. Include safety measures relevant to specific steps. Color-code activities by department or responsibility area to clarify ownership.
Add reference links to related procedures or documentation. Use consistent symbols that match your company standards for flowcharting. Test your maps with actual workers to verify accuracy before finalizing.
Well-designed process maps make complex procedures immediately understandable, reducing training time and improving adherence to standards across your manufacturing floor.
4. Involve Relevant Stakeholders
Engaging the right people ensures your SOPs reflect reality and gain acceptance throughout your organization. Include operators who perform the tasks daily, as they understand practical challenges and effective workarounds that management might miss. Involve maintenance personnel who can advise on equipment capabilities and limitations.
Consult quality control staff who can identify critical inspection points and measurement techniques. Include safety officers to ensure hazard controls are properly integrated. Meet with production supervisors who understand how the procedure fits into broader workflows.
Consider involving vendors or equipment manufacturers who can provide technical specifications. Schedule focused workshops where stakeholders can review draft procedures and provide immediate feedback. Create mechanisms such as employee surveys for anonymous input to capture concerns people might hesitate to voice publicly.
Document all stakeholder input systematically, showing how each contribution was addressed in the final SOP. This collaborative approach results in procedures that work in practice, not just in theory.
5. Draft the SOP
Structure your SOP with clear organization that workers can easily follow during actual operations. Create a standardized template with consistent formatting across all company procedures. Begin with document control information including title, ID number, revision date, and approval signatures.
Write the purpose statement explaining why the procedure exists and what problem it solves. Define terminology specific to the procedure to prevent misunderstandings. List all tools, parts, materials, and reference documents needed to complete the tasks. Write instructions using an active voice and present tense for clarity.
Break complex tasks into numbered sub-steps with no more than 10 steps per section. Include warnings before steps where errors could cause safety issues, quality problems, or equipment damage.
Add notes explaining the reasoning behind critical steps. Insert photos, diagrams or screenshots at points where visual guidance helps understanding. Use consistent terminology throughout, avoiding acronyms or jargon that might confuse new employees.
6. Review and Test
Before implementation, thoroughly test your draft SOP in actual working conditions. Have someone unfamiliar with the process attempt to follow the instructions exactly as written to identify gaps or unclear directions. Conduct structured walkthroughs with supervisors and experienced operators to spot technical errors or omissions.
Compare the SOP against applicable regulations and standards to verify compliance. Check alignment with related procedures to prevent conflicts or contradictions. Evaluate the document against established company writing standards and formatting requirements. Verify that safety precautions adequately address all identified hazards.
Time the completion of tasks following the SOP to ensure timeframes are realistic. Test the procedure under various operating conditions to confirm it works in all scenarios. Document all feedback systematically and prioritize revisions based on safety impacts and operational importance.
Make necessary adjustments before final approval, then conduct a final verification test of the revised version. This rigorous review process prevents costly errors and ensures your SOPs are practical, accurate tools for daily operations.
7. Implement and Train
After approval, launch your new SOP with proper training and support. Create training materials that complement the SOP with examples and demonstrations of correct technique. Schedule dedicated training sessions as part of effective onboarding rather than simply distributing the document.
Develop competency assessments that verify workers can perform the procedure correctly. Designate experienced employees as procedure coaches who can mentor others during the transition period. Provide laminated quick-reference guides for workstations showing key steps and safety information.
Create videos demonstrating proper execution of complex tasks that supplement written instructions. Schedule follow-up sessions to address questions after workers have had time to use the new procedure. Establish a feedback mechanism for reporting problems or suggesting improvements.
Monitor compliance during the initial implementation period, providing immediate correction for deviations. Recognize and reward proper adherence to build positive reinforcement. Document training completion for compliance purposes and to track which employees are qualified to perform the procedure.
8. Establish Regular Updates
SOPs must evolve with your manufacturing processes to remain effective. Schedule automatic review dates at regular intervals, typically every 6-12 months. Assign specific responsibility for maintaining each SOP to prevent documentation from becoming outdated.
Create a formal change management process for updating procedures when equipment, materials, or regulations change. Implement a version control system that tracks revisions and ensures only current versions are available on the production floor.
Collect ongoing user feedback through suggestion programs, observation, and performance data analysis. Monitor process metrics to identify when procedures may need optimization. Document the justification for all changes to maintain an audit trail. Require formal sign-off from management, quality, and safety departments for significant revisions.
Communicate updates promptly to all affected personnel through multiple channels. Provide refresher training when major changes occur. Archive obsolete versions for reference and compliance purposes while ensuring they cannot be accidentally used.
Accessibility of SOP in Manufacturing Industry
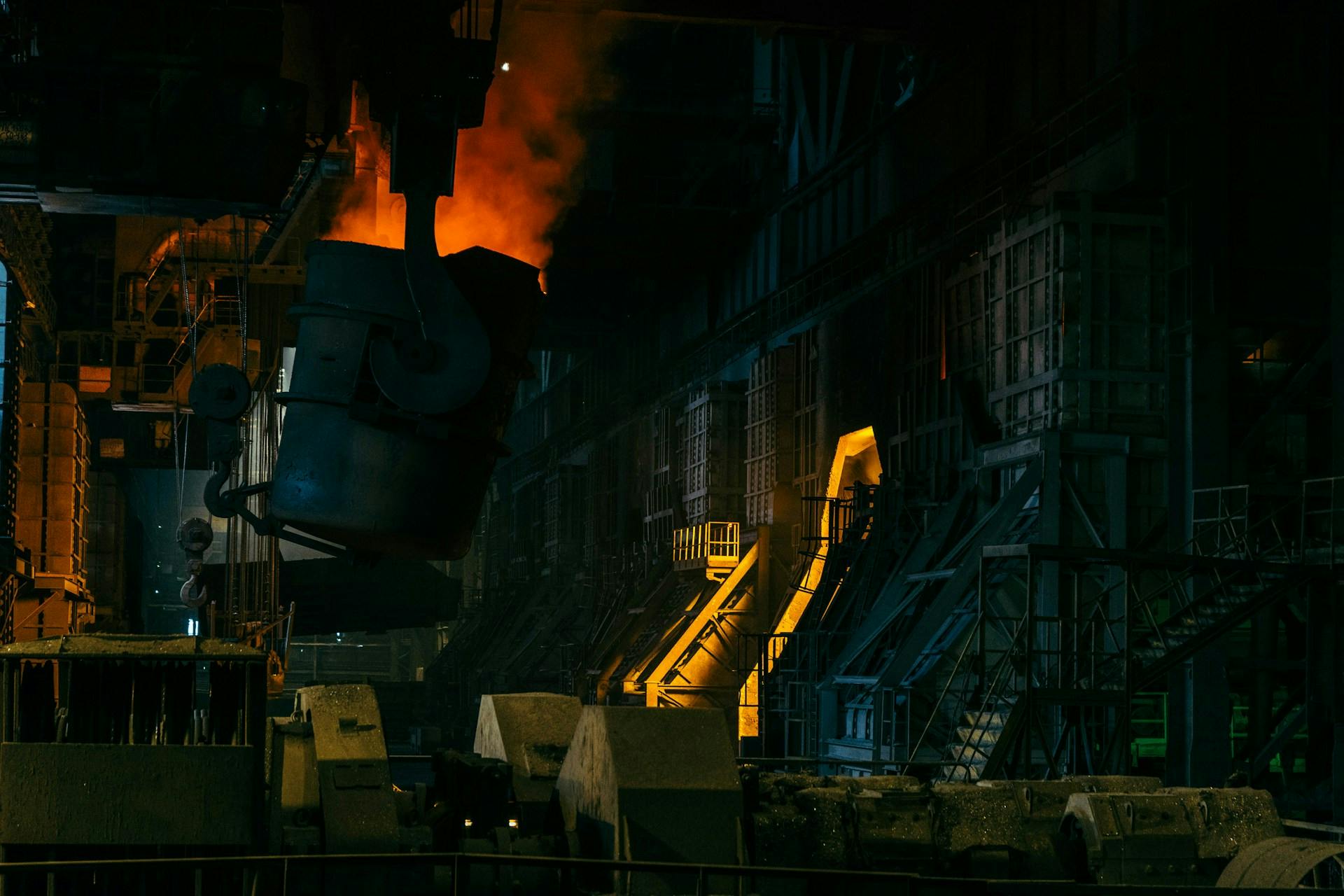
Proper accessibility is important for effective SOP implementation across your organization. Simply distributing SOPs without a thoughtful implementation strategy often leads to poor adherence and confusion.
Making SOPs Highly Visible
Making SOPs readily available at the point of use significantly improves adherence rates in manufacturing environments. Install weatherproof documentation stations directly on the production floor where operators can quickly reference procedures without leaving their workstations.
Create color-coded quick reference guides that extract the most essential information for common tasks, laminated for durability in industrial settings. Convert complex procedures into visual work instructions using photographs of your actual equipment rather than generic illustrations.
Implement digital display screens at workstations that show relevant procedures based on the current production run. Use QR codes on equipment that link directly to applicable procedures when scanned with a tablet or phone.
Post large-format visual workflow diagrams in work cells showing process sequences. Install digital kiosks in break areas where workers can review procedures during downtime. Label storage locations for tools and materials to match terminology used in SOPs.
Technology for Enhanced SOP Management
Leveraging technology and IT tools in training can dramatically improve how you manage and implement SOPs in the manufacturing industry:
- Implement a digital, automated knowledge database or wiki instead of difficult-to-update PDFs
- Look for software that integrates with your existing tools.
- Use workflow automation to ensure SOPs are executed consistently, reducing the risk of errors
- Implement monitoring tools that provide real-time insights into adherence and areas for improvement
Collecting feedback from employees and encouraging their involvement in SOP development fosters buy-in and creates a culture of continuous improvement.
Enhancing Communication of SOP in Manufacturing Industry to Frontline Workers
Manufacturing companies face challenges getting SOPs to frontline workers who rarely access computers. Traditional methods like bulletin boards and paper manuals often fail to reach all employees. Implementing efficient communications strategies solves this problem by delivering SOPs directly to workers' personal phones.
SMS-based systems ensure immediate delivery of procedure updates, safety protocols, and production changes to everyone simultaneously, enhancing multi-locational efficiency. Workers receive consistent instructions regardless of shift or location, improving compliance rates across facilities.
Modern SMS platforms like Yourco enhance internal communications by enabling instant two-way SMS communication, allowing workers to confirm receipt of SOPs, ask clarifying questions, or report safety and operational issues directly via text. With Yourco, you can send documents directly to your employees’ phones via links and they can access these documents securely using a one-time password connected to their phone number. Moreover, with HRIS and payroll integrations, when an employee no-longer works for your company, access to these documents will accordingly be revoked.
Addressing Non-Compliance Risks with SOP in Manufacturing Industry
Non-compliance in business can lead to severe consequences that impact your organization's financial health, operations, and reputation. The specific risks you face depend on several factors: the area of business affected, the type of violation, the severity and frequency of non-compliance incidents, and your company's previous compliance history.
The most significant risks of non-compliance include:
- Financial penalties: Monetary fines are among the most common consequences and can range from minor to substantial, depending on the violation.
- Operational disruptions: In extreme cases, particularly those involving unsafe working conditions or environmental violations, authorities may force you to cease some or all business operations.
- Legal consequences: Beyond civil penalties, certain compliance failures can trigger criminal charges, especially in cases of fraud, theft, or severe environmental violations.
- Reputational damage: Perhaps the most long-lasting impact is the erosion of customer trust and market position, affecting your business's long-term sustainability.
To mitigate these risks effectively, consider implementing these strategic approaches:
- Establish clear policies and procedures that align with federal, state, and local requirements
- Conduct regular compliance training for managers and employees
- Implement robust documentation and recordkeeping systems
- Stay informed about regulatory changes and update your policies accordingly
- Perform regular compliance audits to identify and address issues before they escalate
- Foster a culture of compliance through transparent communication and consistent enforcement of policies
Proactive compliance isn't just about avoiding penalties—it sets your business up for long-term success by building efficiency, safety, and trust into your operations.
Measuring SOP Effectiveness in Manufacturing Industry
To truly understand if your Standard Operating Procedures are delivering results in the manufacturing industry, you need to implement a structured measurement system using Key Performance Indicators (KPIs). When developing KPIs to evaluate your SOPs, follow these best practices:
- Keep KPIs aligned with your overall business objectives. Each SOP should contribute to specific organizational goals, not just exist as documentation.
- Focus on quality over quantity. Start with a few targeted KPIs rather than attempting to measure everything, which simplifies implementation and increases adoption.
- Make them actionable and accountable by setting clear targets and designating responsible team members who can influence the related processes.
- Ensure KPIs are attainable within your available resources to prevent derailing your improvement initiatives.
- Review and refine regularly to maintain relevance and maximize benefits.
Effective SOP Metrics
When measuring SOP effectiveness in manufacturing or operations environments, consider these powerful metrics:
- Perfect Order Metric (POM): Measures the percentage of customer orders delivered complete, on time, damage-free, and with correct invoicing. This comprehensive metric directly reflects how well your SOPs are performing across multiple departments. A high POM indicates effective SOPs across your fulfillment chain.
- Throughput: Tracks the quantity of goods produced over a specific time period, helping you assess if your SOPs are optimizing manufacturing productivity. Calculating good units produced divided by total time provides insight into process efficiency.
- Capacity Utilization Rate: Shows the percentage of total output capacity being utilized, which helps determine if your SOPs are enabling teams to maximize available resources. A rate approaching 100% suggests your SOPs are driving efficient operations.
Connect Your Workforce with Yourco
SOPs only work when they reach your frontline workers. Manufacturing environments need reliable communication systems that connect management with employees who don't sit at desks or regularly check email.
Yourco's SMS-based employee app solves these problems by delivering SOPs directly to workers' phones through simple text messages, helping to engage deskless workers and improve team communication.
Without requiring special apps or training, Yourco ensures everyone receives critical procedure updates, can confirm receipt, and access information when needed—connecting your entire workforce with the information they need to maintain quality and safety standards.
Try Yourco for free today or schedule a demo and see the difference the right workplace communication solution can make in your company.