10 Rules for Workplace Safety Every Manager Should Know
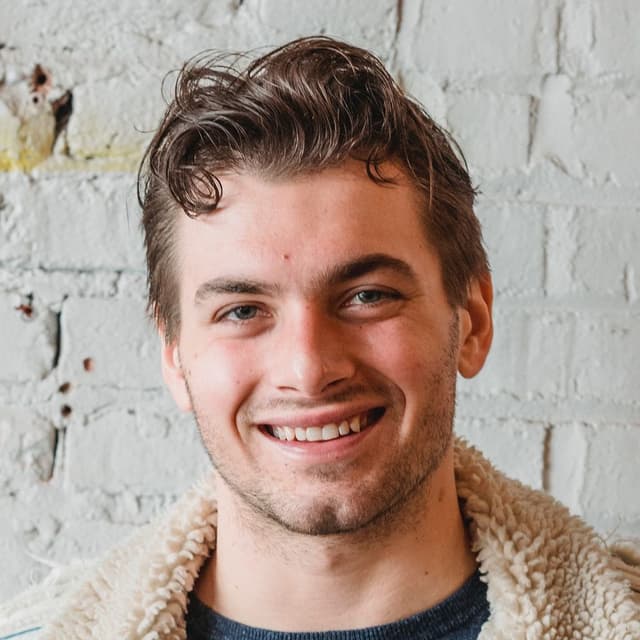
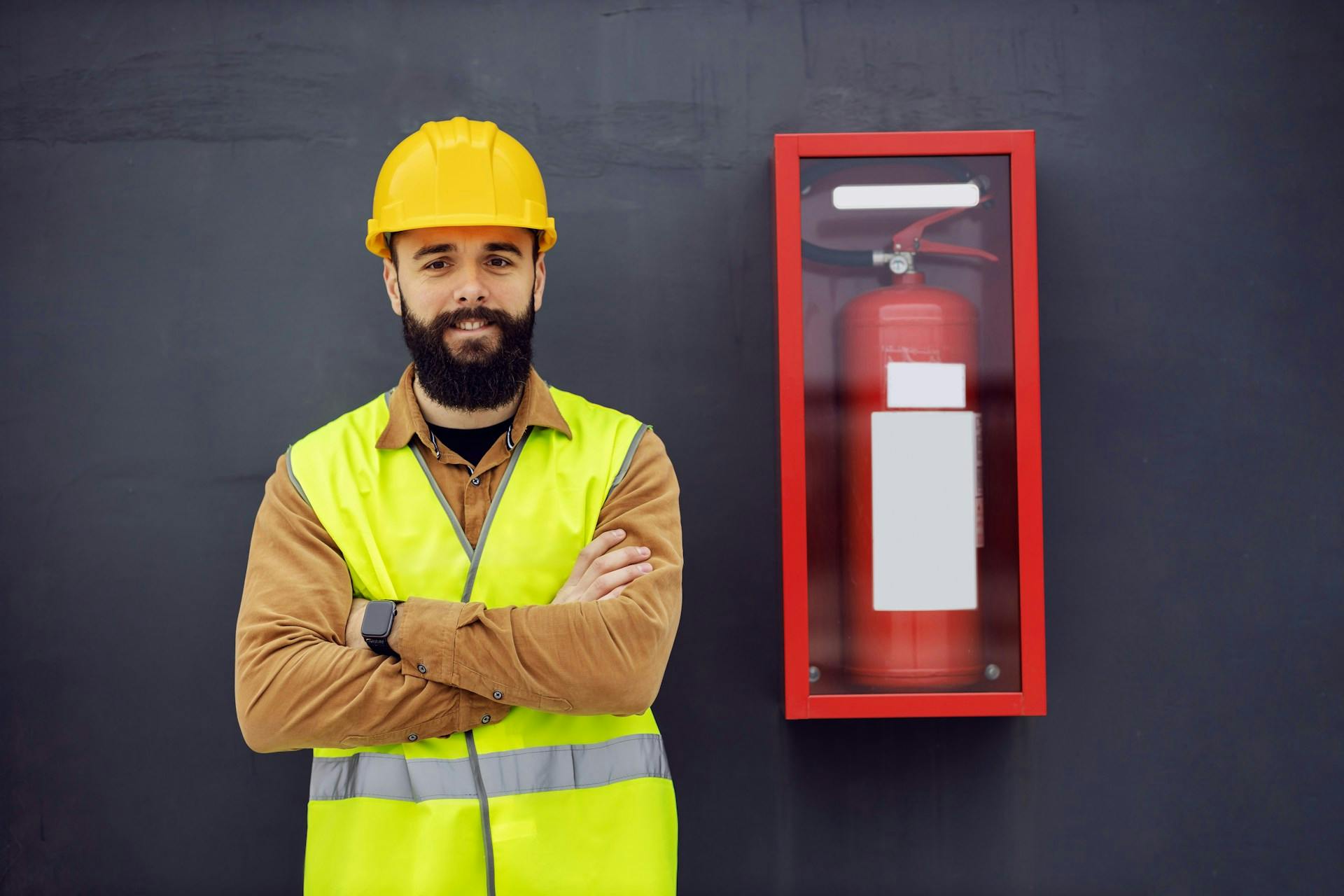
Workplace safety is more than just a set of guidelines—it's a culture that protects your most valuable assets: your employees. For managers overseeing non-desk workers in industries like manufacturing, construction, and logistics, safety protocols are the backbone of daily operations. Reducing accidents not only ensures the well-being of your team but also boosts productivity and morale. Here are 10 essential workplace safety rules every manager should know to create a safer, more efficient work environment.
1. Implement Proper Safety Training and Documentation
Proper safety training is the cornerstone of accident prevention in industrial settings. Think of it as giving your team the tools they need to stay safe and sound. Your training program should mix a thorough onboarding process with regular refresher courses, zeroing in on role-specific hazards and emergency procedures. According to SafetyCulture, daily safety briefings and toolbox talks are essential for keeping safety protocols fresh in employees' minds.
Document all training activities meticulously and maintain digital records of attendance, certifications, and competency assessments. To ensure clear understanding across your diverse workforce, consider using an SMS-based employee communication platform like Yourco, which is capable of delivering safety quizzes in multiple languages. Send scheduled reminders for certification renewals and upcoming training sessions via SMS, achieving a 98% read rate compared to traditional email communications.
For effective implementation, break down complex safety procedures into micro-training segments delivered through text messages. Use a mix of formats—photos, written procedures, and interactive quizzes—to reinforce learning. Track completion rates and comprehension through Yourco's analytics dashboard so you can identify areas needing additional focus or clarification.
2. Maintain Clean and Organized Work Areas
A cluttered workspace isn't just an eyesore—it's an accident waiting to happen. Keeping work areas clean and organized is essential for preventing slips, trips, and falls, which are among the leading causes of workplace injuries. Implement a "clean as you go" policy where workers tidy up immediately after completing tasks. Ensure walkways and emergency exits are clear, and have designated spots for tools and materials.
Create a daily cleaning schedule that includes:
- Morning workspace inspection
- Mid-shift cleanup of accumulated debris
- End-of-day organization check
- Immediate response to spills or hazards
Use clear labeling systems for storage areas and maintain a minimum 3-foot clearance around emergency equipment and exits. Designate specific zones for different activities and materials, and make sure all items are returned to their proper places after use. A systematic approach to workplace organization not only prevents accidents but also improves operational efficiency.
3. Establish Clear Emergency Procedures
Every facility needs robust emergency procedures that consider the mobile nature of non-desk workers. Your emergency response plan should spell out specific actions for scenarios like fires, chemical spills, or medical emergencies. Start by mapping out evacuation routes and assembly points for each work area, making sure they're clearly marked and easy to access.
Designate safety leaders for each department or shift who can coordinate responses and account for personnel. These leaders should be easily identifiable and trained in emergency protocols, including how to sound alarms and use emergency equipment like fire extinguishers.
For operations spread across multiple locations, it's essential to standardize your emergency procedures while accounting for site-specific hazards. Incorporating employee alerts through SMS communications ensures that critical information reaches your workforce promptly. Text messages boast an impressive read rate and quick response time, making them an effective tool for alerting employees about emergency protocols.
To leverage these advantages, consider using Yourco's SMS-based employee communication platform. Yourco seamlessly delivers safety alerts and emergency notifications in multiple languages, ensuring clear understanding across your diverse workforce. With features like scheduled reminders and real-time translations, Yourco ensures that every employee receives and acknowledges important safety information without delay.
Conduct regular emergency drills—think of them as dress rehearsals that make the real thing less dramatic. Use these opportunities to test your emergency notification systems and identify potential gaps in your procedures. After each drill, gather feedback from your non-desk workers about what worked and what needs improvement. This hands-on approach helps refine your procedures while keeping safety awareness high among your mobile workforce.
4. Implement Proper Equipment Operation Protocols
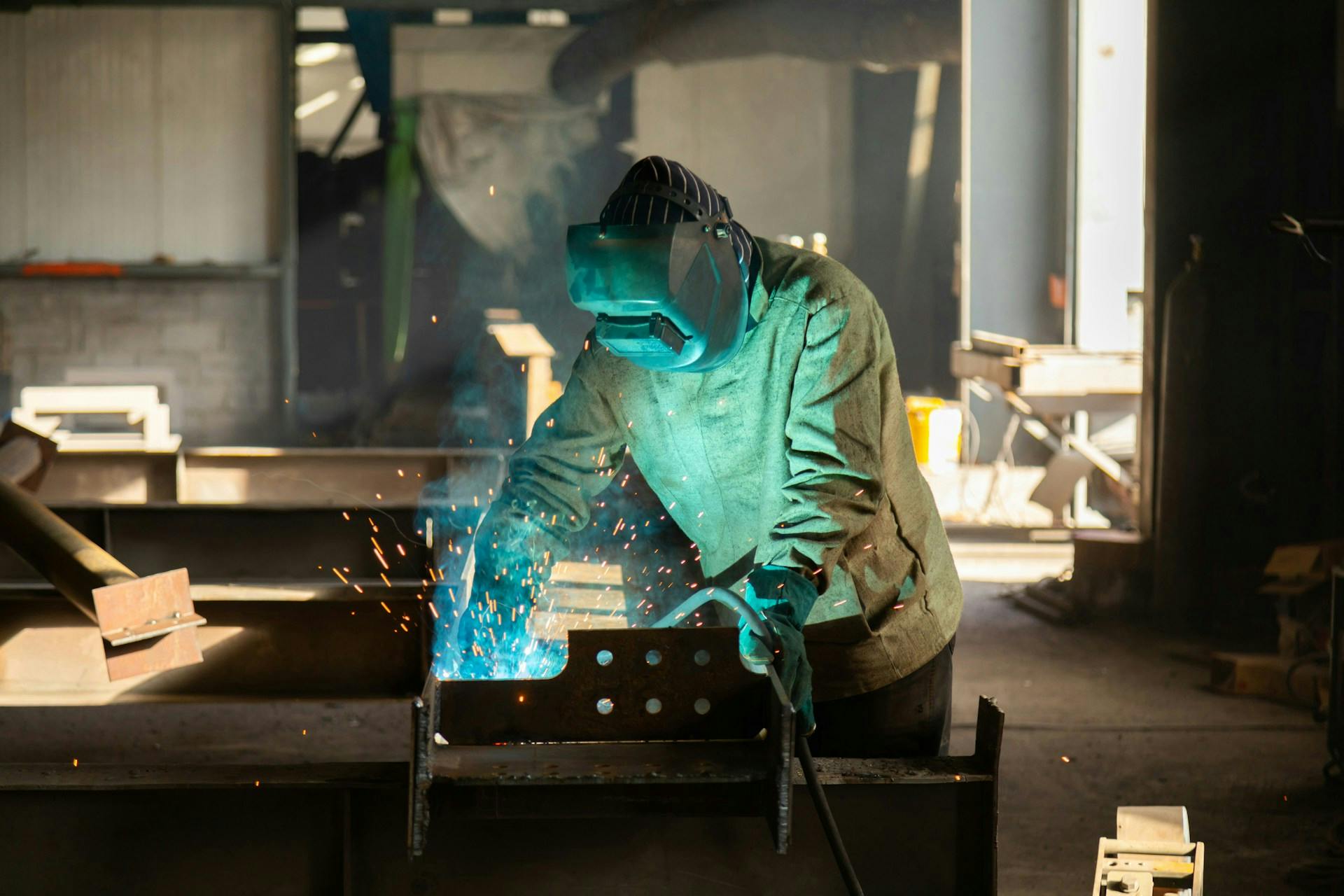
Operating equipment safely demands strict protocols to prevent accidents and maintain standards. Only authorized and properly trained personnel should operate machinery, with current certifications tracked and verified before access is granted. All equipment must be used according to manufacturer specifications, with operator manuals readily available for reference.
Implement a regular maintenance schedule with digital tracking systems to ensure timely inspections and repairs. Machine guards and safety devices must remain in place at all times—never remove or bypass these critical protections. When equipment malfunctions occur, operators must immediately stop use and report defects to maintenance staff through proper channels. Document all maintenance activities and equipment issues in a centralized system for tracking and compliance purposes.
To maintain safe operations, schedule routine operator recertification and conduct periodic assessments of equipment-specific competencies. Regular recertification and competency assessments ensure your workforce maintains the necessary skills while keeping your equipment running safely and efficiently.
5. Create Hazard Reporting Systems
Setting up an accessible hazard reporting system is crucial for preventing workplace accidents. Offer multiple ways to report issues, including anonymous options and text-based solutions, so all workers can easily raise safety concerns. With text messages having a 98% read rate and a 90-second average response time, SMS-based reporting through platforms like Yourco enables field workers to instantly alert supervisors about potential hazards without needing desktop access.
Your reporting system should include clear procedures for documenting hazards, automatic escalation protocols for serious risks, and a tracking mechanism for follow-up actions. Encourage reporting by creating a no-blame culture where workers feel comfortable raising concerns without fear of reprisal. Most importantly, demonstrate the system's effectiveness by responding swiftly to reported hazards and communicating the actions taken—this builds trust and promotes continued use of the reporting system.
6. Enforce Proper Body Mechanics and Ergonomics
Preventing strains and sprains in non-desk work environments means focusing on how tasks are performed. Train your team to lift with their legs, not their backs, and to keep heavy loads close to their body. For jobs that involve doing the same movements over and over, mix things up with job rotations and encourage short breaks to keep everyone feeling their best.
Make mechanical aids like pallet jacks, dollies, and lift assists readily available and mandatory for loads exceeding 50 pounds. Schedule regular ergonomic assessments of common tasks, particularly in manufacturing and warehousing areas where repetitive motions are frequent. Reinforce proper techniques through daily toolbox talks and hands-on demonstrations, focusing on industry-specific scenarios like proper positioning when operating machinery or handling materials on production lines.
Remember, ergonomic improvements often come from worker feedback—encourage your team to report tasks that cause discomfort before they lead to injuries. Use this information to modify workstations and processes for better body alignment and reduced strain.
7. Maintain Substance-Free Workplace Policies
In manufacturing and industrial settings where employees operate heavy machinery and perform safety-sensitive tasks, maintaining a substance-free workplace is fundamental to preventing accidents. Implement and enforce clear policies that include pre-employment screening, random drug testing, and reasonable suspicion procedures. However, effective substance-free policies should go beyond just testing by establishing comprehensive employee assistance programs that provide confidential support for workers struggling with substance use issues.
Your policy should clearly communicate that substance use severely impairs judgment and motor skills, significantly increasing accident risks. Make sure to outline specific procedures for reasonable suspicion testing while emphasizing that the goal is maintaining workplace safety, not punishment. Using Yourco's communication platform, you can regularly remind workers about both policy requirements and available support resources to ensure everyone stays informed and supported.
8. Schedule Regular Safety Audits and Inspections
Regular safety audits and inspections are your first line of defense against workplace accidents. Implement a structured inspection schedule that includes daily equipment checks, weekly area inspections, and monthly comprehensive facility audits. Use detailed checklists that cover all critical areas: machinery conditions, PPE availability, emergency equipment accessibility, and proper signage placement.
Document every inspection thoroughly, including photos of potential hazards and detailed notes about necessary corrections. Track completion of corrective actions to ensure nothing falls through the cracks. This thorough documentation provides a clear record for compliance purposes and helps identify patterns that might indicate underlying safety issues.
By proactively identifying and addressing risks through regular inspections, you can prevent many accidents before they occur. Make these inspections collaborative by involving employees from different departments—their hands-on experience often helps spot potential hazards that might otherwise go unnoticed.
9. Develop Effective Safety Communication Systems
When lives are on the line, communicating safety protocols quickly is key. Utilize multiple communication channels, primarily SMS, since 90% of text messages are opened within 5 minutes. Digital displays in break rooms and physical bulletin boards can reinforce critical safety information.
Keep safety updates brief and frequent rather than lengthy and sporadic. For instance, send quick reminders about PPE requirements at the start of shifts or alert workers about specific hazards as they're identified. Consider implementing a dedicated safety hotline where workers can report concerns immediately.
Digital solutions like Yourco's SMS-based employee communication platform are particularly effective for enhancing employee communication, as they allow you to track message delivery and engagement. Yourco enables organizations to deliver safety updates in real-time, ensuring that 85% of deskless workers receive and understand crucial safety information. With AI-powered translations, Yourco ensures that safety protocols are clearly communicated across a diverse workforce, eliminating language barriers.
Additionally, Yourco's scheduled reminders and automated follow-ups help maintain consistent communication without overwhelming employees. Features like secure document access allow workers to easily reference safety manuals and guidelines directly from their mobile devices. By leveraging Yourco, organizations can ensure that important safety protocols are not only delivered promptly but also acknowledged and understood by every team member.
10. Implementation and Monitoring
Start by establishing baseline safety metrics and setting clear goals for improvement. Roll out new safety rules through a combination of formal training sessions and regular SMS updates via Yourco's platform. Use visual aids throughout your facility and reinforce rules through daily toolbox talks.
Monitor compliance through regular safety audits and leverage Yourco's polling features to gather real-time feedback from workers, and consider announcing survey results to foster engagement. Track key metrics like incident rates, near-miss reports, and hazard identification submissions. Create accountability by assigning safety champions at each level of the organization.
Make adjustments based on collected data and employee input, carefully interpreting survey results to identify areas for improvement. Use Yourco's automatic translation feature to ensure safety communications reach all workers in their preferred language. Remember that successful safety programs evolve—regularly review and update your rules based on new insights and changing workplace conditions.
Elevate Your Safety Protocols with Yourco
Implementing these safety rules is just the beginning. To truly transform your workplace safety, you need a communication tool that keeps everyone connected, informed, and engaged—no matter where they are. That's where Yourco comes in. As the #1 SMS-based employee app designed for the non-desk workforce, Yourco enables you to send timely safety updates, schedule training reminders, and gather real-time feedback effortlessly. With its unparalleled 98% read rate, you can be confident that critical information reaches your team instantly. Plus, features like automatic translation ensure that language barriers don't stand in the way of safety. By integrating Yourco into your safety strategy, you're not just reducing accidents—you're building a culture of safety that empowers every worker. Ready to make your workplace safer and more connected?
Try Yourco for free today or schedule a demo and see the difference the right workplace communication solution can make in your company.