Safety Compliance with Effective Operating Procedures
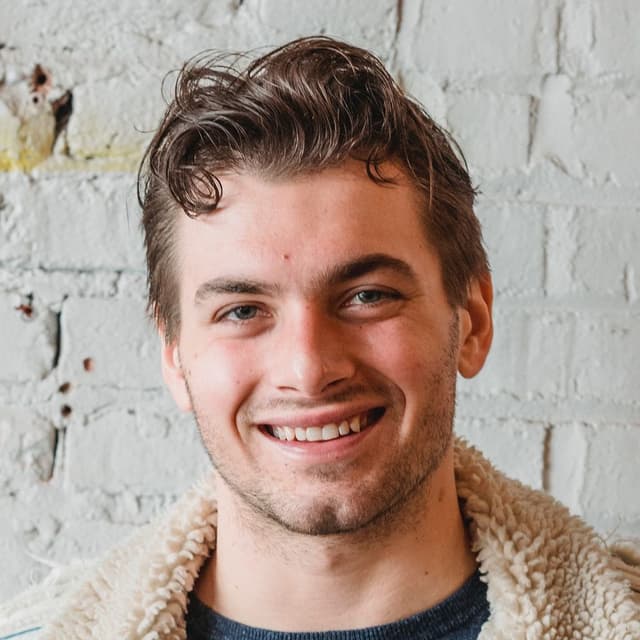
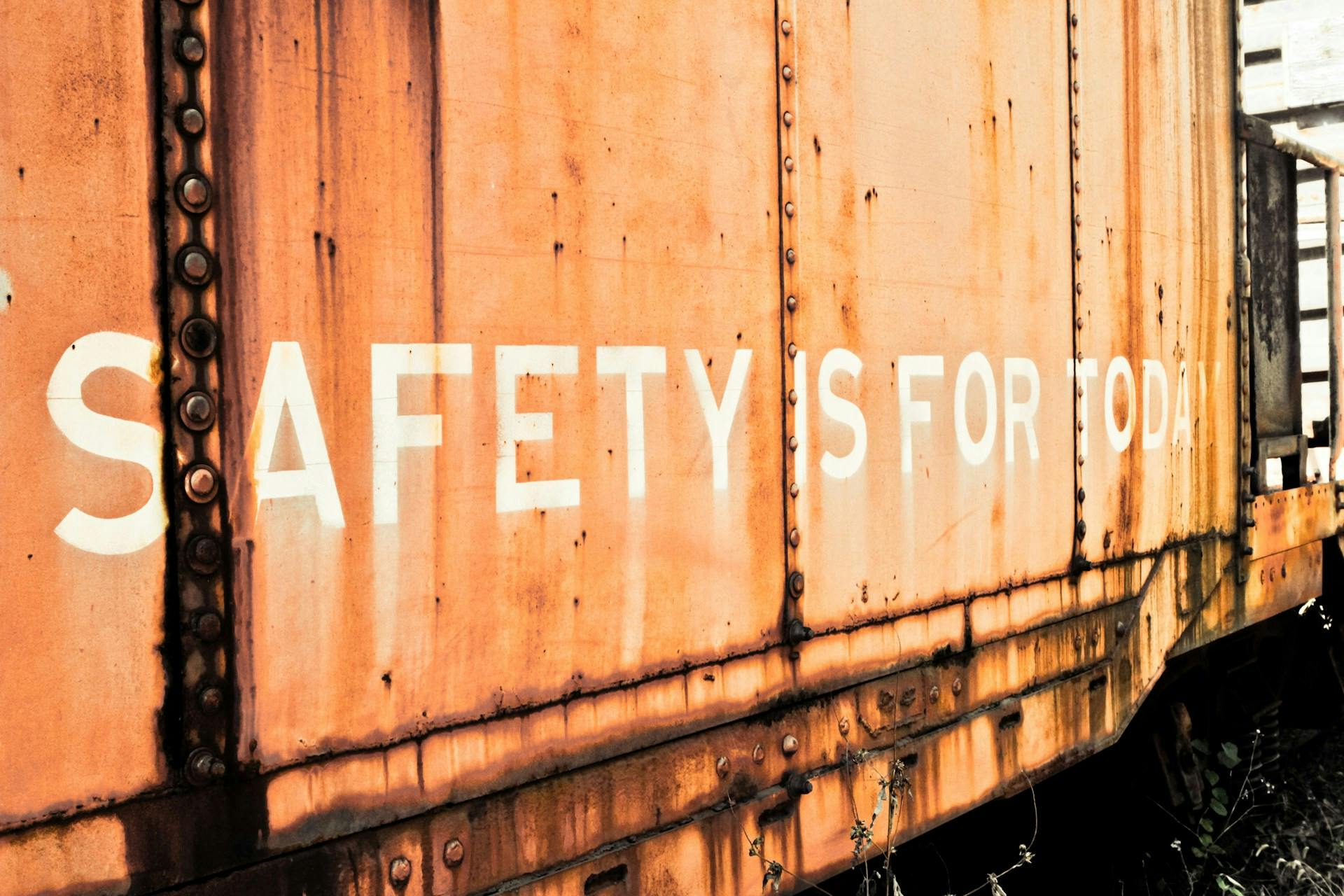
Safety operating procedures (SOPs) are detailed, documented workflows that standardize how high-risk tasks should be performed to minimize safety hazards. For non-desk workers in manufacturing, construction, and healthcare, these procedures protect lives daily.
These workers face unique physical risks, with 38.4% fatal falls occurring in construction alone in 2022. Well-designed safety operating procedures transform regulations into actionable processes while ensuring consistency across workers and shifts.
Beyond employee protection, these procedures help organizations meet OSHA requirements and other regulatory standards, reducing accidents and creating safer, more efficient workplaces.
Safety Operating Procedures: Beyond Basic Guidelines
Safety operating procedures (SOPs) are formal, written instructions that define the correct way to perform specific tasks to minimize risk and ensure consistency. Unlike general workplace guidelines, safety operating procedures provide detailed, step-by-step directions for completing activities safely, particularly in high-risk environments.
Safety professionals will tell you that safety operating procedures aren't suggestions—they're mandatory protocols designed to protect workers and ensure regulatory compliance. This distinction matters for any organization building a comprehensive safety program.
Main Characteristics of Effective Safety Operating Procedures
Safety operating procedures differ significantly from general workplace guidelines in several important ways:
- Specificity: Safety operating procedures address particular tasks or processes, while guidelines cover broader workplace principles.
- Detail Level: Safety operating procedures provide comprehensive, step-by-step instructions, whereas guidelines offer general direction.
- Structure: Safety operating procedures follow a standardized format that typically includes:
- Purpose and objectives to clarify the procedure’s importance.
- Scope (who, when, and where the procedure applies) to define applicability.
- Detailed procedural steps ensuring consistent execution.
- Hazard identification and safety precautions to prevent incidents.
- Required equipment and personal protective equipment (PPE) for worker protection.
- References to related procedures or regulations to maintain compliance.
- Review and update protocols to ensure ongoing relevance and effectiveness.
Industries Where Safety Operating Procedures Protect Worker Safety
Non-desk work environments benefit from formal safety operating procedures due to their higher risk profiles. Industries where safety operating procedures play an important role include:
- Manufacturing, where machinery operation carries significant risks
- Construction, with changing job sites and numerous hazards
- Healthcare, where procedures affect patient safety
- Chemical processing, where hazardous materials are present
- Transportation and logistics, with equipment and vehicle operation risks
In these environments, the detailed nature of safety operating procedures provides several advantages that general guidelines cannot. They create consistency across shifts and locations, ensuring all workers follow the same safe procedures.
They also serve as valuable training tools, particularly for new employees unfamiliar with equipment or processes. Finally, they provide explicit instructions for emergency situations when clear thinking may be compromised.
For non-desk workers, the specificity of safety operating procedures addresses the physical risks they face daily. While general guidelines might state "use appropriate safety equipment," an effective safety operating procedure will specify exactly which PPE is required for a particular task, how to inspect it before use, and how to wear it properly.
How Safety Operating Procedures Protect Employees in High-Risk Environments
In non-desk environments, where physical hazards are ever-present, safety operating procedures serve as a defense against workplace accidents and injuries. In 2022, the construction industry accounted for nearly one in five workplace fatalities, with falls, slips, and trips comprising 38.4% of these deaths.
Specifically, there were 412 fatal falls, slips, and trips in construction that year, with 397 resulting from falls to a lower level. These numbers highlight why comprehensive safety operating procedures aren't just paperwork—they're lifesaving tools.
Preventing Workplace Accidents Through Standardized Procedures
Safety operating procedures create consistency in how tasks are performed, which directly reduces the likelihood of accidents. When every worker follows the same carefully designed process, human error—a leading cause of workplace incidents—decreases significantly.
In high-risk industries, this standardization matters for:
- Machine operation and maintenance, preventing entanglement, crushing injuries, and amputations by ensuring proper use of guards and emergency shut offs.
- Fall protection systems, especially on construction sites where falls remain a leading cause of fatalities, by mandating harness inspections and secure anchor points.
- Chemical handling procedures, minimizing exposure to hazardous substances through clear labeling, storage guidelines, and proper PPE usage.
- Lockout/tagout protocols, preventing electrical accidents by ensuring equipment is fully de-energized before maintenance begins.
Ensuring Proper Training and Hazard Awareness
Safety operating procedures serve as foundational training tools that build hazard awareness among employees. Well-designed procedures:
- Identify specific risks associated with each task, ensuring workers understand potential hazards before starting work.
- Outline required personal protective equipment (PPE), including proper fit and usage to maximize protection.
- Detail proper techniques that avoid ergonomic injuries, such as correct lifting methods and posture recommendations.
- Specify emergency response procedures, ensuring workers know how to react swiftly and correctly when things go wrong.
Organizations transform safety from an abstract concept into concrete, actionable steps that employees can implement daily through these procedures. This approach works well for new workers who may not yet recognize the dangers inherent in their environments, helping them develop safe habits from day one.
Building a Culture of Safety and Accountability
The most powerful long-term benefit of comprehensive safety operating procedures is their ability to develop a culture of safety and accountability. When safety procedures are clearly documented, regularly updated, and consistently enforced, they send a message that safety isn't optional—it's a core value.
This cultural shift occurs because safety operating procedures:
- Clearly define safety responsibilities at all levels of the organization
- Provide objective standards against which performance can be measured
- Create common language and expectations around safety
- Establish frameworks for reporting hazards and near-misses
Additionally, by supporting employee mental health, organizations further strengthen their safety culture, ensuring employees feel valued and engaged.
The accountability aspect matters in high-risk environments where one person's unsafe actions can endanger others. With well-implemented safety operating procedures, you're not just protecting individual workers—you're creating a system where everyone plays an active role in maintaining a safe workplace.
How Safety Operating Procedures Improve Regulatory Compliance
Safety operating procedures play an important role in helping organizations meet regulatory requirements and maintain a safe work environment. When properly implemented, safety operating procedures serve as the backbone of your regulatory compliance strategy, especially in industries with non-desk workers, while also enhancing workplace efficiency.
Meeting OSHA, ISO, and Industry-Specific Requirements
Safety operating procedures help organizations stay compliant with regulatory standards incorporating specific requirements directly into everyday work processes. Rather than treating compliance as an afterthought, well-designed safety operating procedures build regulatory requirements into the fabric of daily operations. This approach ensures that:
- Employees follow OSHA regulations as part of their routine tasks, reducing the risk of citations and penalties.
- ISO quality standards are consistently maintained across all operations, improving efficiency and reliability.
- Industry-specific requirements are clearly communicated and implemented, ensuring that workers understand and adhere to the latest safety laws.
- Documentation and reporting processes align with compliance mandates, making audits smoother and reducing liability in case of inspections or incidents.
Documentation and Proof of Safety Protocols
One of the most valuable aspects of safety operating procedures is that they provide tangible evidence of your commitment to safety and compliance. During regulatory inspections or audits, well-documented procedures demonstrate that your organization has established formal processes to meet requirements.
Safety operating procedures serve as important documentation:
- Providing evidence that safety measures are in place, reinforcing your organization’s proactive approach to risk management.
- Demonstrating that employees have been properly trained, ensuring that safety protocols are understood and consistently followed.
- Showing a systematic approach to hazard identification and risk mitigation, reducing workplace incidents.
- Establishing a record of continuous improvement in safety practices, proving that safety is an ongoing priority rather than a one-time effort.
Reducing Liability and Insurance Costs
Beyond meeting regulatory requirements, safety operating procedures play a significant role in reducing organizational liability and controlling insurance costs. Standardizing safe work practices, these procedures can:
- Decrease the frequency and severity of workplace accidents, fostering a safer work environment and minimizing disruptions.
- Reduce workers' compensation claims, leading to lower costs and fewer long-term disability cases.
- Lower insurance premiums through demonstrated safety practices, showing insurers that risk mitigation measures are in place.
- Provide protection in the event of litigation, serving as documented proof of due diligence.
Furthermore, in the event of an accident, having comprehensive safety operating procedures in place demonstrates that the organization took reasonable steps to prevent injuries. This documentation can prove invaluable in limiting liability and defending against negligence claims.
Effective Communication Strategies for Safety Operating Procedures
Getting safety operating procedures into the hands of non-desk workers presents unique challenges, especially when many employees have limited or no regular computer access. To ensure these safety guidelines reach everyone, organizations must employ a diverse range of effective communication strategies that meet workers where they are.
Overcoming Limited Computer Access
For employees without regular computer access, mobile-first communication methods like text messaging offer an especially effective channel for safety information.
SMS has emerged as a particularly powerful tool, with a 98% open rate within the first five minutes. This makes it ideal for urgent safety updates or reminders about procedures.
Text messaging provides a direct line to workers' phones without requiring them to download anything, making it accessible even for less tech-savvy workers. Implementing employee texting solutions ensures that safety information reaches everyone on your team.
Multi-Format Approaches (Digital, Print, Visual)
The most effective safety operating procedure communication strategies utilize multiple formats to ensure information reaches and resonates with all employees.
Visual aids like infographics and posters placed in high-traffic areas can convey safety information at a glance and help overcome language barriers.
Despite our digital world, print materials remain essential. Pocket guides containing safety procedures provide workers with portable references they can carry with them.
For multilingual workforces, implementing inclusive communication strategies such as providing safety documentation in all languages spoken by your employees is necessary. Supporting these materials with bilingual safety liaisons who can bridge language gaps ensures clear communication of safety information.
Training and Reinforcement Strategies
Face-to-face communication remains one of the most effective ways to ensure understanding and compliance with safety operating procedures.
Toolbox talks—brief meetings at the start of shifts focused on specific safety topics—can reinforce procedures regularly. A logistics company that implemented daily 5-minute toolbox talks saw a 50% increase in proactive safety reporting from employees over six months.
Designating and training employees to serve as safety ambassadors is one way of improving team communication and creating peer-to-peer communication channels that can be incredibly effective. As workplace safety expert Dr. Michael Johnson notes, "When employees see their colleagues championing safety, it creates a culture of accountability."
Collecting Feedback and Measuring Understanding
Effective safety operating procedure communication doesn't end with dissemination—organizations need mechanisms to verify understanding and gather employee input.
Anonymous reporting systems encourage employees to report safety concerns without fear of repercussions. Regular safety surveys can gauge employee understanding of procedures and collect suggestions for improvement.
As safety consultant Tom Wilson explains, "Two-way communication is essential. Employees on the front lines often have valuable insights into how safety procedures can be improved."
Organizations should also implement recognition programs that reward employees for consistently following safety operating procedures and contributing to a safer workplace. Positive reinforcement can be a powerful motivator for safety compliance.
The most successful safety communication strategies combine multiple approaches tailored to the specific needs of the workforce. Using a mix of traditional and modern communication methods ensures that safety information reaches all employees, regardless of their access to technology, engaging non-desk workers, creating a stronger culture of safety and reducing workplace incidents.
Measuring the Impact of Safety Operating Procedures
Implementing safety operating procedures is just the beginning—measuring their effectiveness drives continuous improvement and ensures workplace safety. Tracking specific metrics helps determine whether your procedures are working as intended and identifies areas that need adjustment.
Performance Indicators for Safety Operating Procedures
To effectively evaluate your safety operating procedures, monitor both leading and lagging indicators:
Leading Indicators (Preventive Measures):
- Training completion rates – Track how many employees have completed procedure training and their assessment scores
- Audit results – Regular safety audits can reveal how well procedures are being followed before incidents occur
- Near-miss reporting – An increase in near-miss reporting often indicates improved safety awareness
- Behavioral observations – Regular observations of work practices can identify compliance with procedures
- Employee feedback – Surveys and feedback sessions about procedure clarity and usability
Lagging Indicators (Outcome Measures):
- Incident rates – Monitor the frequency and severity of workplace accidents
- Lost time injuries – Track injuries that result in lost workdays
- Compliance violations – Record instances where regulatory standards weren't met
- Workers' compensation costs – Measure financial impact of workplace injuries
- Equipment damage – Note frequency and cost of equipment damage related to improper procedures
The most effective measurement systems use a combination of both types of indicators to provide a comprehensive view of procedure effectiveness.
Using Measurement Data to Improve Procedures
Once you've collected performance data, the next step is using it to drive improvements:
- Identify patterns and trends – Look for commonalities in incidents or near-misses that might indicate procedure weaknesses.
- Prioritize high-risk areas – Focus improvement efforts on procedures related to the most serious or frequent incidents.
- Involve employees in revisions – Those who perform the tasks daily often have the best insights for improving procedures.
- Document improvements – Track changes made to procedures and measure their impact on safety metrics.
- Share success stories – When improvements lead to positive outcomes, communicate these wins to reinforce the importance of safety operating procedures, boosting morale and encouraging continued safety focus.
Safety That Sticks
Well-implemented safety procedures do more than meet regulations—they significantly reduce workplace incidents, cut costs, and improve productivity. Clear guidelines help workers adopt safe practices naturally, making them active participants in safety efforts.
How Yourco Can Help
Yourco offers a robust, SMS-based platform that streamlines the management of safety documentation, incident reporting, and insurance claims, making it an ideal solution for non-desk workers across various industries such as manufacturing, construction, healthcare, and logistics.
No apps, no complicated software—employees just text.
- Snap and Send: Workers quickly take a photo of any injury, damage, or unsafe condition using their phones.
- Real-time Descriptions: They text the image along with a brief explanation directly to the company’s dedicated Yourco number.
- Immediate Logging: Yourco timestamps and securely stores each message instantly, ensuring accuracy and timeliness.
This simple, intuitive process encourages immediate reporting, drastically reducing delays or forgotten details common with traditional paperwork.
Once an incident report is logged, HR managers or safety officers can instantly access the documented details from a secure and centralized system. Managers can easily reply via SMS to request additional information or clarifications directly from the reporting employee, making follow-up conversations simple, immediate, and efficient.
This real-time, two-way communication strengthens incident management, ensuring safety issues are addressed rapidly and thoroughly without manual paperwork or lengthy email chains.
Moreover, Yourco doesn’t just simplify reporting—it enhances regulatory compliance, making safety audits smoother and more efficient.
- All incident reports and safety communications are securely stored and fully searchable.
- Yourco provides easily retrievable evidence that the company actively complies with OSHA and industry-specific regulations.
- Accurate documentation protects the company legally, clearly demonstrating proactive safety measures and reducing liability.
By combining instant accessibility via SMS, centralized documentation, and secure data storage, Yourco effectively transforms safety compliance from a cumbersome manual process into a streamlined, proactive safety management solution.
Try Yourco for free today or schedule a demo and see the difference the right workplace communication solution can make in your company.