On-Site Safety Tips for Deskless Workforces
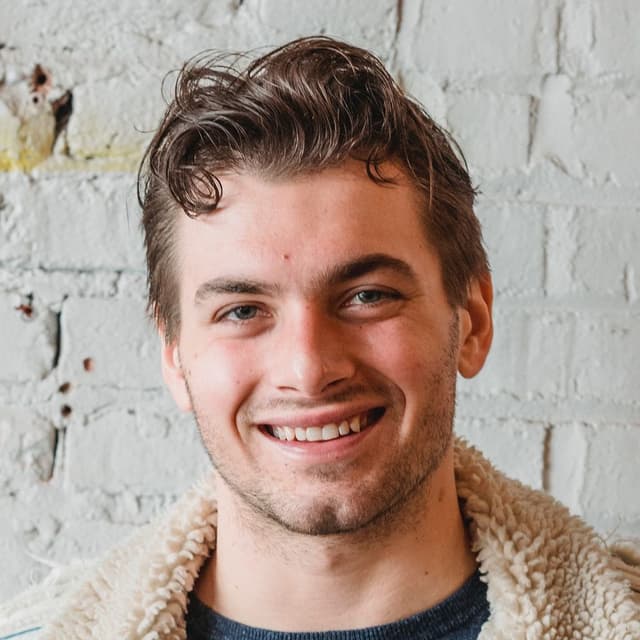
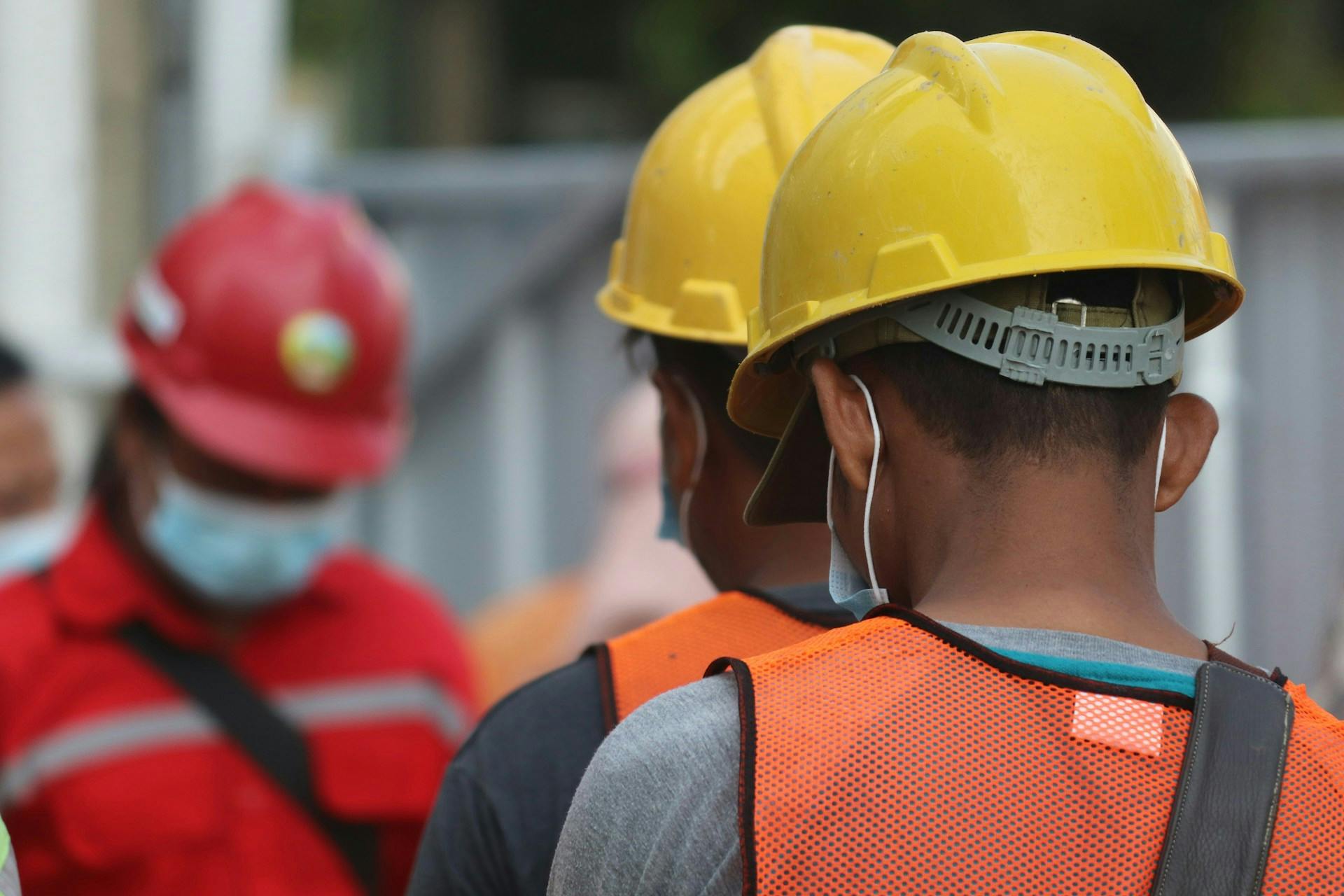
On site safety matters for organizations with distributed field workers who encounter different hazards than office employees. For workers in construction, manufacturing, and logistics, safety directly affects individual wellbeing, organizational performance, and compliance requirements. Managing safety across multiple locations demands effective communication systems tailored to workers' specific needs.
The statistics are sobering: falls from heights caused 320 out of 1,008 construction fatalities in a year. These numbers highlight why safety protocols must address the specific risks field workers face daily, while organizations navigate regulatory frameworks like OSHA standards that apply regardless of where teams operate.
Common On Site Safety Challenges for Non-Desk Employees
Non-desk workers face safety challenges unlike those of office-based employees. Understanding these challenges helps create effective systems to protect your workforce.
Physical Hazards Impacting On Site Safety
Falls from heights remain one of the most significant safety risks for field workers. According to the Bureau of Labor Statistics, falls are the leading cause of fatal workplace injuries. In 2018, falls from heights accounted for 320 out of 1,008 construction fatalities in the United States.
Organizations can reduce this risk through proper guardrails, safety nets, fall arrest systems, and comprehensive training on prevention techniques, as well as adhering to established workplace safety rules.
Struck-by hazards present another major concern, accounting for about 14% of construction worker fatalities in 2022. These incidents typically involve workers being hit by moving vehicles, falling objects, or flying debris. Clear traffic management plans, high-visibility clothing, and proper barriers between work zones significantly reduce these risks.
Environmental and Exposure Risks Affecting On Site Safety
Chemical exposure poses significant risks to field workers across industries. Manufacturing workers encounter toxic fumes or corrosive materials, while agricultural workers face dangers from pesticides. Proper ventilation systems, appropriate PPE, and training on hazardous material handling serve as protective measures.
Noise-induced hearing loss affects millions of workers annually. According to the U.S. Centers for Disease Control and Prevention (CDC), approximately 22 million workers are exposed to potentially damaging noise at work each year. Prolonged exposure to noise levels above 85 decibels can lead to permanent hearing loss.
Engineering controls to reduce noise at the source, appropriate hearing protection, and regular hearing tests help protect workers in high-noise environments. Heat stress threatens workers in outdoor environments or hot indoor settings, particularly affecting construction workers, agricultural laborers, and warehouse workers.
Prevention strategies include shaded rest areas, access to water, scheduling heavy work during cooler parts of the day, and implementing heat illness prevention plans.
Communication and Coordination Challenges in On Site Safety
For field workers, effective communication often faces obstacles from distance, noise, and technological limitations. Many work sites have poor cell reception or internet connectivity, making real-time communication difficult during emergencies.
Redundant communication systems, including two-way radios and satellite phones for remote locations, help address this challenge. Coordination between different teams and contractors on large work sites presents another safety challenge. When multiple groups work in close proximity without proper coordination, accident risks increase.
Implementing solutions for team communication, including clear communication protocols, regular safety briefings, and a centralized communication system improves coordination and reduces risks.
Language barriers create significant safety challenges in diverse workforces. Workers with limited proficiency in the primary language may misunderstand safety instructions or struggle to communicate hazards effectively.
Safety materials in multiple languages, visual communication aids, and a buddy system for non-native speakers help overcome language barriers.
Remote and lone workers face unique communication challenges as they may lack immediate access to help during emergencies. Check-in systems, GPS tracking, and panic buttons on mobile devices provide these workers with necessary safety support.
Building Effective Safety Communication Systems for On Site Safety
Creating effective safety communication systems, by implementing best practices for safety communication, makes a significant difference between a safe workday and a preventable incident for field workers. Field teams need specialized approaches to ensure safety.
Mobile-First and Multi-Channel Communication Enhancing On Site Safety
Implementing effective communication tools for deskless workers is important because field workers rarely access desktop computers during their workday, making a mobile-first approach necessary. This includes:
- Responsive Design - Ensures accessibility across all devices, from smartphones to tablets.
- Low-Bandwidth Options - Allows seamless communication in areas with weak internet connections.
- Offline Capabilities - Enables workers to access critical information even without an internet connection.
- Push Notifications - Delivers urgent alerts instantly to employees' devices.
A multi-channel approach ensures safety messages reach workers regardless of location:
- Using a text messaging service for businesses for alerts
- Digital signage in break areas
- Radio communication for areas with poor cell coverage
Real-Time Alert and Notification Systems
When safety conditions change rapidly, immediate communication becomes necessary. Real-time alert systems, like SMS notifications for safety, provide:
- Instant Notifications – Quickly inform employees about emerging hazards to prevent accidents.
Weather Alerts – Warn workers of extreme conditions that could impact worksite safety. - Equipment Failure Warnings – Notify relevant teams about malfunctioning machinery to prevent downtime or injuries.
- Emergency Evacuation Instructions – Deliver clear, step-by-step guidance during crises.
The best systems allow for audience segmentation, ensuring messages reach the right people—such as specific teams, shifts, or locations—without overwhelming others. Integration with other workplace safety tools can further enhance response times and improve overall safety management.
Two-Way Communication and Feedback Mechanisms
Safety communication requires input from field workers. Implementing strong employee communication strategies creates an environment where field workers can easily communicate safety concerns, leading to faster hazard resolution and a safer workplace.
Effective two-way communication systems include:
- Reporting Tools – Allow workers to quickly report hazards before they escalate.
- Quick-Access Emergency Buttons – Provide immediate alerts for urgent situations.
- Photo and Video Upload Capabilities – Enable workers to document unsafe conditions with visual evidence.
- Voice Messaging Options – Ensure communication remains efficient when typing isn’t practical.
When field workers can easily report safety concerns, organizations gain real-time insights from those closest to potential hazards. This continuous feedback loop strengthens safety protocols and reduces workplace risks, and creates instant documentation that can be referenced later when filing an insurance claim.
It reduces the delay in getting incident reports—no waiting until the end of the day or forgetting—and helps protect the company in case of a dispute by showing the exact moment and context of the event. HR or the safety manager can follow up to gather more details, ensuring a prompt and thorough response to any issues.
Accessibility and Inclusive Communication
Field workforces often include diverse workers with varying language proficiency, technical literacy, and physical abilities. Implementing strategies for overcoming language barriers is essential. Inclusive safety communication incorporates:
- Multilingual Support – Provides translations for employees who speak different languages.
- Simple, Clear Language – Avoids jargon and complex terms to improve comprehension.
- Visual Elements – Uses icons, infographics, and color-coded alerts to reinforce messages.
- Accessibility Features – Includes text-to-speech options, high-contrast visuals, and alternative formats for workers with disabilities.
An effective safety communication system combines these elements to connect management and field personnel. By making communication clear and accessible, organizations create environments where hazards are quickly identified, reported, and addressed.
Developing a Comprehensive On Site Safety Program
Traditional office-based safety approaches don't work for distributed field teams. Structured processes must function across multiple locations.
Risk Assessment for Distributed Workforces
A strong safety program begins with risk assessment tailored to field operations, helping to prevent accidents and create a safer work environment:
- Job Safety Analysis (JSA) – Develop standardized frameworks that break down field tasks, identifying potential hazards and control measures. Regularly update JSAs to reflect new risks or process changes.
- Site-Specific Hazard Identification – Establish protocols for recognizing hazards unique to each work location, including environmental factors, equipment-specific risks, and seasonal conditions that may impact safety.
- Risk Prioritization – Implement a consistent scoring system to assess risks based on severity and likelihood, ensuring high-risk issues are addressed first.
Regular safety audits, worker feedback, and technology-driven reporting tools further enhance risk assessment, allowing organizations to stay ahead of potential hazards.
Documentation and Reporting Systems
Field workers need simple ways to document safety information to ensure quick reporting and efficient hazard management.
- Mobile-First Approach – Make safety documentation accessible via smartphones or tablets from any location, allowing workers to report issues in real time without returning to an office.
- Standardized Forms – Use consistent reporting forms for hazards, near-misses, and incidents that field workers can complete quickly. Digital forms with dropdown menus, checkboxes, and voice-to-text options improve efficiency.
- Cloud-Based Storage – Establish a centralized system where all safety documentation remains easily retrievable. Secure access ensures compliance with regulatory requirements and allows managers to analyze trends over time.
Regular training on documentation procedures helps workers feel confident in reporting, creating a culture of safety and accountability.
Training Protocols for Remote Teams
Classroom training doesn't suit distributed workforces, making it important to adopt flexible, accessible methods for onboarding non-desk employees. Effective non-desk employee onboarding requires alternative approaches such as:
- Microlearning – Break safety training into short, engaging modules completed in 5-10 minutes on mobile devices. This approach helps workers retain information without feeling overwhelmed.
- Scenario-Based Training – Use real-world scenarios specific to field operations, reinforcing hazard recognition and safe decision-making.
- Just-in-Time Learning – Make task-specific safety information available on-demand before performing unfamiliar tasks, reducing the risk of errors.
- Virtual Reality/Augmented Reality – For high-risk operations, simulation training presents dangerous situations without endangering workers, allowing them to practice responses in a safe environment.
Providing multilingual options and easy access to training resources helps employees feel more prepared for their roles.
Emergency Response Planning
Every worksite needs clear emergency procedures to keep workers safe and ensure a quick response during unexpected situations. Well-prepared teams can minimize risks and reduce confusion when emergencies arise:
- Emergency Action Plans (EAP) – OSHA requires workplaces with more than 10 employees to have written plans. These should include evacuation routes, assembly points, and designated roles.
- Site-Specific Emergency Procedures – Customize plans for each location’s unique layout, hazards, and proximity to emergency services, ensuring all risks are addressed.
- Emergency Communication Chain – Establish clear communication lines for different emergency types, emergency notification systems, text alerts, and radios to ensure swift dissemination of information.
- Regular Drills – Conduct emergency response drills, including fire, medical, and severe weather scenarios, so workers can practice executing plans effectively.
Providing multilingual emergency instructions and easily accessible safety guides further strengthens preparedness.
Hazard Communication Programs
OSHA requires industries using hazardous chemicals to implement written Hazard Communication Programs (HCP) to protect workers and ensure safe handling practices. A well-structured program reduces risks and helps employees recognize and respond to potential hazards. HCP requirements include:
- Written and distributed to all employees – Ensure every worker understands the program and their role in chemical safety.
- Include a complete chemical inventory – Maintain an up-to-date list of all hazardous substances used on-site.
- Provide access to Safety Data Sheets (SDS) – Workers must be able to review chemical properties, health risks, and safety precautions.
- Outline proper labeling procedures – Clearly mark containers with hazard warnings and handling instructions.
Detail training requirements for chemical handling – Conduct regular training sessions to reinforce safe practices. - Make this information accessible via mobile devices and keep physical copies at each worksite – Ensure employees can quickly reference safety guidelines when needed.
Regular program updates and compliance checks further strengthen workplace safety.
OSHA Reporting Requirements
Safety programs must include protocols for meeting OSHA's reporting requirements to ensure compliance and prompt response to workplace incidents:
- Report work-related fatalities within 8 hours – Immediate reporting allows OSHA to assess the situation and provide guidance if needed.
- Report work-related inpatient hospitalizations, amputations, or losses of an eye within 24 hours – Timely reporting ensures proper investigation and corrective actions.
- Train supervisors on these requirements and establish backup reporting chains – Educate managers on the process to avoid delays, and designate alternate personnel to ensure reporting continues during absences.
Implementing digital reporting tools, maintaining accurate incident logs, and conducting regular compliance reviews help streamline the process and reinforce accountability in workplace safety.
Continuous Improvement Cycles
Safety programs need regular updates to remain effective and responsive to evolving workplace hazards:
- Regular Audits – Schedule periodic safety audits of field operations to identify potential risks and ensure adherence to safety protocols.
Incident Analysis – Analyze all incidents and near-misses to identify root causes, implement corrective actions, and prevent future occurrences. - Feedback Mechanisms – Create ways for field workers to suggest safety improvements, such as anonymous reporting systems or safety meetings.
- Quarterly Reviews – Conduct formal reviews of your safety program, updating procedures based on incident data, employee feedback, and regulatory changes.
- Annual Program Evaluation – Perform comprehensive assessments measuring effectiveness against established metrics, including injury rates, compliance levels, and worker participation.
Industry-Specific Applications and Best Practices
Safety needs vary dramatically across industries, requiring tailored approaches for different operational environments.
Construction: Multi-Site Safety Management
Construction companies manage safety across constantly changing job sites with diverse teams and subcontractors.
Challenges include:
- Coordinating protocols across numerous sites – Ensuring consistent safety standards while adapting to unique site conditions.
- Managing temporary and subcontracted workforces – New workers need quick onboarding and ongoing training to align with company safety policies.
- Communicating in noisy environments – Traditional methods may be ineffective, requiring visual signals, digital alerts, and mobile communication tools.
- Addressing varying literacy levels and languages – Multilingual safety materials, visual aids, and audio-based training improve comprehension.
Best practices include daily toolbox talks through mobile applications, QR codes at entry points providing site-specific information, and clear emergency communication protocols.
Manufacturing: Connecting Plant Floor and Field Teams
Manufacturing environments present challenges in connecting factory floor workers with remote maintenance and support teams.
Challenges include:
- Noisy environments inhibiting verbal communication – Visual alerts, text-based updates, and vibration-based notifications improve message delivery.
- Complex machinery requiring specialized safety protocols – Operators need easy access to digital safety manuals and real-time troubleshooting guides.
- Shift work creating communication gaps – Shift handover logs and mobile updates ensure seamless information flow between teams.
- Need for rapid response to equipment malfunctions – Automated alerts help reduce downtime and prevent accidents.
Modern safety systems integrate IoT sensors with mobile alerts. When a machine detects irregular operation, it automatically triggers alerts to both on-site operators and remote maintenance personnel.
Best practices include visual communication boards displaying real-time safety metrics, digital work order systems with safety checklists, and dedicated communication channels for each production line.
Utilities and Field Service: Ensuring Lone Worker Safety
Utility and field service workers often operate independently in remote locations, making reliable safety communication essential for their well-being.
Concerns include:
- Workers operating alone in isolated areas – Increases risks if an accident occurs without immediate assistance.
Exposure to environmental hazards – Extreme weather, wild animals, and hazardous terrain pose threats. - Limited connectivity in remote regions – Weak signals make real-time communication difficult.
- Extended emergency response times – Delays in assistance can escalate minor incidents into serious situations.
Effective safety communication combines GPS tracking, panic buttons, and automated check-in systems. Many utilities use wearable technology monitoring both worker vitals and environmental conditions.
Best practices include regular virtual check-ins, geofencing to alert supervisors when workers enter high-risk areas, and backup communication methods for limited connectivity areas.
Transportation and Logistics: Mobile Workforce Protection
The transportation and logistics industry faces unique challenges with its highly mobile workforce navigating changing environments.
Challenges include:
- Personnel working independently across wide geographic areas – Drivers and field workers often operate without direct supervision.
- Constantly changing environmental and traffic conditions – Weather, road closures, and congestion impact schedules and safety.
- Risk of fatigue during long shifts – Extended driving hours increase accident risks.
- Limited ability to access information while operating vehicles – Drivers must stay focused on the road while receiving updates.
Effective systems focus on timely, hands-free delivery of information. Voice-activated systems allow drivers to receive and report safety information without diverting attention from the road.
Best practices include pre-trip safety briefings through mobile apps, automated rest reminders preventing fatigue, and clear emergency communication protocols.
Safeguarding Your Workforce with SMS Communication
Safety systems for field operations must create a genuine safety culture beyond compliance. Organizations that implement systematic, technology-enabled approaches protect workers while achieving compliance, operational efficiency, and financial benefits through reduced incidents and lower insurance premiums.
If you're still using email, bulletin boards, or word-of-mouth for safety information, your workforce faces unnecessary risk. Non-desk workers need communication tools designed for mobile environments. Yourco's SMS platform connects field workers regardless of location or tech familiarity.
Text messages boast a 98% open rate, ensuring safety alerts are immediately seen. Safety managers can send targeted alerts, receive confirmation, and collect incident reports through simple text exchanges—no special apps required.
With Yourco, employees can snap a picture of an injury, property damage, or unsafe conditions and send it via text to the company's dedicated Yourco number. That message becomes part of the internal incident record, timestamped and stored, creating instant documentation that can be referenced later for insurance claims or dispute resolution.
This seamless integration helps ensure that safety issues are reported in real time, reducing delays and improving response times. Each safety protocol implemented through Yourco helps workers stay informed and return home safely.
Try Yourco for free today or schedule a demo and see the difference the right workplace communication solution can make in your company.