Health and Safety Compliance in the Workplace
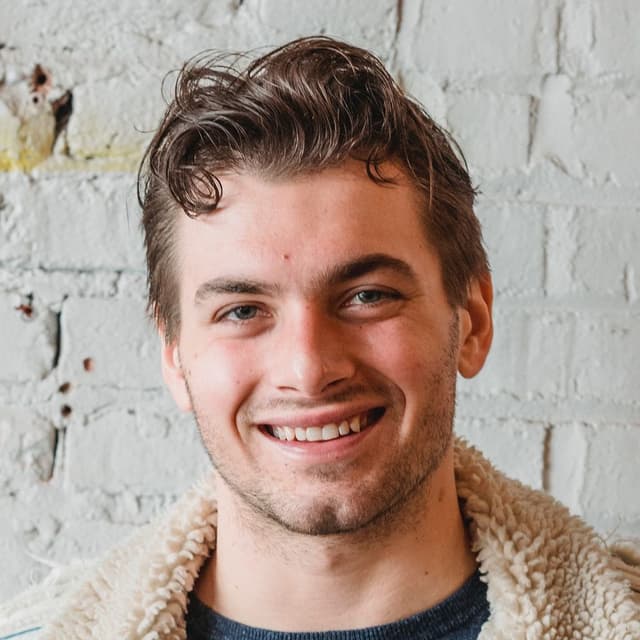

Health and safety compliance means adhering to laws and standards that protect workers from workplace hazards. These regulations help prevent injuries, illnesses, and fatalities.
Health and safety compliance involves more than checking boxes—it creates an environment where everyone performs their duties safely. When companies prioritize workplace safety, they demonstrate commitment to employee wellbeing while strengthening organizational foundations.
Regulatory Framework and Legal Requirements for Health and Safety Compliance
Health and safety compliance operates under numerous standards and regulations that vary across the globe. If your operations span multiple locations or industries, knowing these frameworks becomes necessary.
Global and Regional Regulatory Bodies in Health and Safety Compliance
Several internationally recognized frameworks shape health and safety compliance worldwide:
- ILO Conventions 155 and 187: These International Labour Organization conventions focus on developing national frameworks for occupational safety and health. They promote continuous improvement through standardized laws, monitoring, and stakeholder engagement as outlined by the International Labour Organization.
- International Health Regulations (IHR): Revised in 2005, the IHR takes an "all-hazards" approach to prevent and control international disease spread. Countries must establish national focal points for WHO communication.
- Global Health Security Agenda (GHSA): This U.S.-led initiative works with over 70 countries to strengthen capacities for preventing, detecting, and responding to global health threats.
Regional approaches vary considerably:
- European Union: Operating under Framework Directive 89/391/EEC, the EU sets minimum safety standards. Employers bear legal responsibility for worker safety and risk management.
- United States: The Occupational Safety and Health Act of 1970 (OSHA) governs workplace safety through inspections and enforcement with penalties and corrective measures.
- Asia-Pacific: Japan implements strict approaches through the Industrial Safety and Health Act, while countries like India struggle with enforcement due to large informal economies.
- Africa: Many African nations follow ILO guidance but face regional differences due to resource limitations. South Africa leads with robust legislation including the Occupational Health and Safety Act of 1993.
Factors creating variations in health and safety compliance standards include:
- Economic considerations: High-income countries typically have more comprehensive safety standards and enforcement.
- Cultural differences: Worker participation in safety policy making varies, with European models emphasizing social dialogue.
- Enforcement capabilities: Developed nations impose penalties for non-compliance, while countries in the Global South may focus more on incentives and voluntary adoption due to resource constraints.
Industry-Specific Health and Safety Compliance Requirements
Different industries face unique health and safety challenges requiring tailored approaches:
- Construction: Requires stringent fall protection measures, equipment safety protocols, and site-specific risk assessments. Utilizing mobile-friendly communication solutions helps in effectively communicating these safety requirements to workers on site.
- Manufacturing: Regulations focus on machine guarding, hazardous material handling, and ergonomic considerations for production workers. Implementing effective compliance strategies for manufacturers is essential to address these challenges.
- Healthcare: Compliance needs center on infection control, patient handling procedures, and protection from biological and chemical hazards.
- Transportation: Safety requirements address fatigue management, vehicle maintenance standards, and emergency response training.
- Service Industries with Distributed Workforces: Face challenges maintaining consistent safety standards across multiple locations, often requiring mobile compliance solutions and standardized reporting systems.
Core Elements of an Effective Health and Safety Compliance Program
Creating a strong health and safety compliance program goes beyond checking regulatory boxes. A truly effective program integrates several components that protect your workforce and create a culture of safety. Here's what should form the foundation of your compliance strategy.
Management Leadership and Employee Participation
When management visibly champions health and safety compliance initiatives, they gain credibility throughout the organization.
Successful strategies include:
- Designating compliance officers or committees with clear authority to enforce policies and track performance metrics
- Dedicating sufficient resources for safety initiatives, including training, equipment upgrades, and hazard mitigation
- Including safety performance in management evaluations to reinforce accountability
- Modeling safe behaviors at all leadership levels to demonstrate commitment
Workers on the front lines often know day-to-day hazards best and can suggest practical solutions. Creating safety committees with diverse role representatives builds ownership, taps into valuable frontline insights, and encourages ongoing dialogue that drives continuous improvement.
Hazard Identification and Assessment
You can't fix what you don't spot. A systematic approach to recognizing workplace hazards prevents injuries and illnesses while improving operational consistency.
Effective identification methods include:
- Regular workplace inspections by trained personnel familiar with safety protocols and environmental factors
- Field-Level Risk Assessments (FLRAs) at job sites to identify real-time, task-specific risks
- Job Hazard Analysis (JHA) to break down tasks and identify risks at each step
- Review of incident data, including near misses, to spot recurring hazards and system weaknesses
- Employee reporting systems that encourage open, non-punitive hazard notification
Assessment should evaluate both severity and probability of potential harm using risk matrices to prioritize your response and allocate safety resources effectively.
Hazard Prevention and Control
Once you spot hazards, address them using the Hierarchy of Controls framework:
- Elimination: Completely removing the hazard (most effective), such as discontinuing dangerous tasks or redesigning processes
- Substitution: Replacing hazardous materials or processes with safer alternatives, like using non-toxic chemicals
- Engineering Controls: Modifying equipment or processes to isolate people from hazards, including machine guards or improved ventilation
- Administrative Controls: Implementing procedures, training, or scheduling to reduce exposure, such as rotating shifts or limiting time near hazards
- Personal Protective Equipment (PPE): Providing PPE as the last line of defense (least effective), including gloves, goggles, and respirators
Document specific control measures for identified hazards, assign responsible personnel, and establish clear implementation procedures with deadlines and training requirements.
Education and Training
Training turns compliance into competence. OSHA emphasizes that hands-on, interactive training works best for non-desk workers. Computer-based training alone won't suffice—workers need opportunities to practice skills and ask questions.
Your training program should:
- Target specific job roles and actual hazards workers face
- Include both initial and refresher sessions as part of the core components of onboarding
- Incorporate hands-on demonstrations and practice
- Allow for questions and clarification
- Verify comprehension through testing or observation
- Be delivered in languages and formats accessible to all workers
Incorporating essential rules for workplace safety into your training ensures employees understand important safety protocols. Remember: interactive sessions with practical applications yield better results than passive learning.
Program Evaluation and Improvement
A health and safety compliance program must evolve to stay effective. Regular evaluation helps identify strengths and weaknesses.
Performance indicators to track include:
- Injury and illness rates
- Near-miss reports
- Safety training completion percentages
- Hazard correction timeframes
- Employee participation in safety initiatives
- Results from workplace inspections
Use both leading indicators (preventive measures like training completion) and lagging indicators (outcomes like injury rates) to see the complete picture of your program's effectiveness.
Review documentation, interview employees, observe workplace practices, and analyze trends in safety data. Look for recurring issues or areas showing consistent improvement. Based on findings, develop targeted action plans with clear timelines, responsible parties, and measurable goals to ensure continuous improvement and sustained compliance.
Overcoming Common Health and Safety Compliance Challenges
Organizations with distributed workforces face unique health and safety compliance hurdles. Here's how to tackle these obstacles while maintaining both compliance and operational efficiency.
Communication Barriers with Distributed Workforces
When your team spreads across multiple locations or stays constantly on the move, traditional communication methods fall flat. Effective communicating safety protocols is important to ensure all workers are informed and compliant.
Effective solutions include:
- Text messaging works: SMS messaging enables frontline workers to receive safety information instantly. Unlike email, text messages reach workers directly without requiring special apps or tech-savviness. Implementing an employee notification system can ensure important updates reach everyone promptly.
- Mix online with hands-on: Blend digital modules with in-person sessions to maximize learning while meeting the realities of distributed teams. This hybrid approach can enhance engaging non-desk workers.
- Schedule regular check-ins: Set consistent touchpoints with remote teams to reinforce safety priorities and address emerging concerns. Utilizing efficient communication strategies can help maintain consistent engagement.
Additionally, overcoming language barriers and taking steps to avoid translation errors are critical to ensure safety messages are accurately conveyed and understood by all employees.
Documentation and Record-Keeping in Health and Safety Compliance
Multiple locations often mean fragmented records and inconsistent processes, creating compliance gaps and increased risk.
Workable solutions include:
- Centralize with digital systems: Cloud-based platforms ensure documentation stays accessible, secure, and standardized across all locations. This prevents duplicated efforts and reduces manual errors.
- Automate where possible: Automation improves accuracy, saves time on manual reviews, and ensures timely record updates. Domino's Pizza cut significant time through streamlined documentation across their distributed facilities.
- Standardize your approach: Create uniform templates and processes for all locations to follow, ensuring consistent record-keeping practices.
- Audit regularly: Schedule periodic internal reviews to verify documentation stays current, accurate, and compliant with evolving standards.
Balancing Compliance Costs with Business Needs
Finding the balance between safety investment and business costs challenges many organizations. The good news? Effective health and safety compliance programs pay for themselves.
Smart approaches include:
- Focus on high-ROI initiatives: Over 60% of chief financial officers reported that each $1 invested in injury prevention returns $2 or more. Put your dollars where they make the biggest safety impact.
- Use technology strategically: Invest in compliance software that simplifies processes. The upfront cost quickly pays off through time savings, avoided penalties, and fewer incident-related expenses.
- Make safety part of your culture: When safety becomes part of your organizational DNA, compliance shifts from box-checking to shared protection and operational excellence.
- Analyze costs vs. benefits: Regularly evaluate your safety initiatives to see which provide the best returns. Adjust your approach based on real data rather than assumptions.
- Share resources: Smaller businesses can pool compliance resources across locations or partner with other small companies to spread costs while maintaining strong practices.
Tackling these challenges with practical, cost-effective solutions helps maintain compliance while supporting broader business goals. Remember: compliance isn't just about avoiding fines—it builds the foundation for operational excellence, employee wellbeing, and sustainable growth.
Building a Culture of Health and Safety Compliance
Creating a truly safe workplace means going beyond simply following regulations. While legal compliance matters, organizations that excel in safety develop something more powerful: a culture where safety becomes instinctive in every decision and action.
Beyond Compliance: Creating a Safety-First Mindset
There's a stark difference between mere compliance and a genuine safety culture. Compliance often creates a "checklist mentality"—a reactive approach where organizations simply meet minimum legal requirements to avoid penalties.
A safety culture weaves safety considerations into daily decision-making at every level. When safety becomes a core value rather than an obligation, employees naturally consider potential risks before taking action, regardless of whether a specific rule exists.
Leaders shape this transformation. When executives consistently prioritize safety in decisions, communications, and resource allocation, they send a powerful message through the organization. As leaders demonstrate safe behaviors and emphasize wellbeing over production targets, employees understand that safety truly matters.
Employee Engagement Strategies
When employees feel personally invested in safety outcomes, they become your strongest allies in preventing incidents. Effective engagement approaches include:
- Safety Committees: Form groups with representatives from different departments and levels to bring diverse perspectives to safety planning. These committees can spot potential hazards, review incidents, and suggest improvements.
- Feedback Channels: Create clear ways for employees to report safety concerns without fear. This might include anonymous reporting, regular safety talks, or digital platforms for flagging issues.
- Give Authority: Allow workers to stop work when they see dangerous situations. DuPont's "Stop Work Authority" program lets any employee halt operations if they spot unsafe conditions, showing trust in workers' safety judgment.
Additionally, implementing employee incentives can motivate workers to engage actively with safety programs.
The impact speaks for itself. Gallup's studies have shown that companies in the top quartile of employee engagement have 70% fewer safety incidents than those in the bottom quartile. When employees feel valued and involved in safety decisions, they naturally watch out for procedures and their colleagues.
Measuring and Celebrating Success
To maintain a safety culture, track progress and recognize achievements. Look beyond counting incidents after they happen:
- Track Proactive Measures: Monitor activities like near-miss reporting, safety suggestion implementation, and training completion. These metrics help catch issues before incidents occur.
- Recognize Good Behavior: Develop meaningful ways to acknowledge safety-conscious actions. This might include performance awards, public recognition for teams that address hazards, or incentives for departments with strong safety records.
- Celebrate Wins: Make safety achievements visible through company communications, milestone celebrations (like days without incidents), and success stories highlighting positive impacts of safety initiatives.
Your metrics should drive positive behaviors, not just measure outcomes. When you track and celebrate the right indicators, you reinforce behaviors that create a safer workplace and demonstrate your commitment to protecting your people.
The journey from compliance to culture takes time, but creates workplaces where safety becomes second nature rather than a regulatory burden. Engaging your workforce, showing leadership commitment, and celebrating success builds a safety culture that protects employees while boosting productivity, morale, and reputation.
Digital Transformation in Health and Safety Compliance
Health and safety compliance is continuously improving, with technology reshaping how organizations manage their regulatory obligations. Digital transformation changes how we approach compliance to make it more efficient, effective, and integrated into daily work.
Compliance Management Software Solutions
Traditional compliance often involves paper documentation, manual tracking, and time-consuming reporting. Modern EHS (Environmental, Health, and Safety) software offers a major upgrade by centralizing and automating these functions.
These platforms typically include:
- Regulation tracking and updates
- Document management
- Audit and inspection capabilities
- Incident reporting and investigation tools
- Task management and reminders
The impact can be dramatic—organizations using compliance platforms report up to 90% less time spent on compliance tasks. This efficiency lets safety professionals focus on preventing risks rather than pushing papers.
When choosing a compliance platform, look for:
- Integration with existing systems like HR software or operational databases
- Customizable workflows matching your specific requirements
- User-friendly interfaces encouraging adoption
- Robust reporting for regulatory submissions and internal analysis
The best implementations ensure the software adapts to your processes, not the other way around.
Mobile Applications for Field Workers
Field workers face unique compliance challenges. They're often disconnected from central systems, working where traditional desktop access isn't possible. Engaging deskless workers via mobile applications bridges this gap, bringing compliance tools directly to workers regardless of location.
These communication tools offer advantages:
- Real-time hazard reporting allows immediate documentation of safety concerns
- Digital access to safety protocols when needed most
- Location tagging for contextual safety information
- Photo and video documentation for incidents or inspections
SMS platforms like Yourco enable direct communication between management and field workers, ensuring safety updates reach those who need them. This helps distributed teams without regular access to company email or intranets.
Data Analytics and Predictive Safety in Health and Safety Compliance
The most transformative aspect of digital compliance tools is generating actionable insights from safety data. Advanced analytics lets organizations:
- Spot trends and patterns in safety incidents or near-misses
- Identify early warning signs of potential issues
- Direct resources to high-risk areas
- Measure the effectiveness of safety programs
Predictive analytics takes this further by using historical data to forecast potential problems before they occur. This shifts from reactive compliance to proactive risk management.
For example, analyzing patterns in equipment maintenance records and safety incidents, predictive models can identify when specific machinery might present safety hazards, allowing for preventive maintenance or additional safety measures.
Focus on meaningful metrics rather than collecting data for its own sake. The most valuable insights come from connecting safety data with operational information to provide context for decisions.
If you're starting a digital transformation in safety compliance:
- Assess your current processes and pain points
- Prioritize solutions addressing your biggest challenges
- Involve end-users in selection and implementation
- Plan for training and change management
- Measure results against both compliance outcomes and operational efficiencies
With thoughtful implementation, technology transforms compliance from a burden into a strategic advantage that protects workers, reduces risks, and contributes to operational excellence.
Health and Safety Compliance in Crisis Situations
When unexpected events like pandemics or natural disasters strike, maintaining health and safety compliance becomes both more challenging and more necessary. Well-planned strategies ensure worker protection even during extraordinary circumstances.
Pandemic Preparedness and Response
The COVID-19 pandemic revealed stark differences in how organizations and countries responded to a major health emergency. According to the CDC Global Health Security, some regions showed remarkable resilience while others struggled with implementation:
- Australia implemented strict workplace safety protocols backed by robust health governance.
- India faced significant challenges enforcing compliance, particularly in informal sectors.
These contrasting examples highlight the importance of preparedness for future health emergencies. To maintain compliance during pandemic situations:
- Develop flexible frameworks that adapt to rapidly changing health guidelines.
- Establish clear communication channels for safety updates.
- Create contingency plans for essential operations with health safeguards.
- Document pandemic-specific risk assessments and mitigation strategies.
- Train employees on emergency health protocols before crises occur.
Natural Disasters and Emergency Response
Natural disasters disrupt normal operations and compliance systems. Planning ahead maintains worker protection during these events. Considerations include:
- Documentation resilience: Back up critical compliance records and ensure they remain accessible during disruptions, through cloud storage or physical redundancies.
- Emergency training: Regular drills and scenario-based training prepare employees to maintain safety protocols during chaotic situations.
- Compliance continuity planning: Identify essential compliance requirements that must continue even during emergencies.
- Post-incident assessment: After any emergency, evaluate thoroughly to identify compliance gaps and address them before the next incident.
Resilient compliance systems integrate safety into your emergency response framework. This means considering how to maintain essential safety standards throughout crisis and recovery phases.
Safeguarding Your Workforce Through Smart Health and Safety Compliance
Effective health and safety compliance creates safer workplaces while boosting productivity and strengthening your company's reputation. Strong safety programs reduce workplace incidents, improve morale, and enhance operational results.
Your health and safety program should address regulatory requirements while building a genuine safety culture. Regular review and updates keep your program relevant as regulations and workplace conditions change.
Yourco helps HR professionals connect with non-desk workers through SMS messaging, ensuring safety communications reach every employee with 98% open rates. This supports distributed teams with direct safety updates, incident reporting, and documentation—all without requiring special apps or technical know-how.
Try Yourco for free today or schedule a demo and see the difference the right workplace communication solution can make in your company.