The Ultimate Guide to Building a Strong Workplace Safety Culture
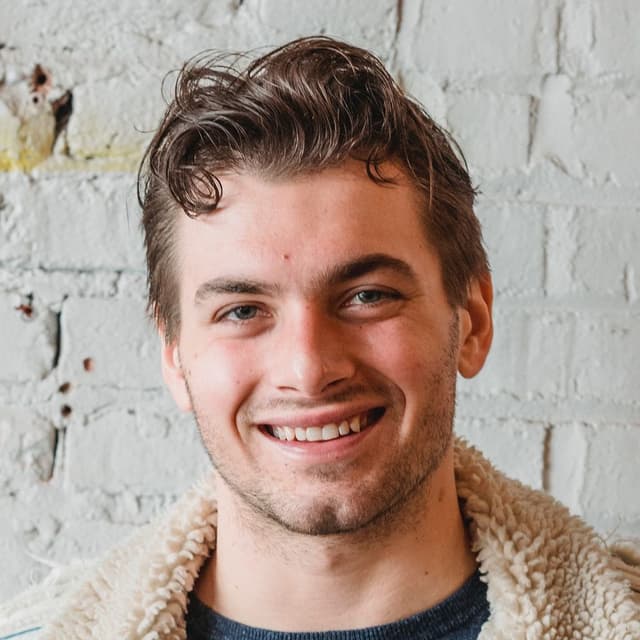
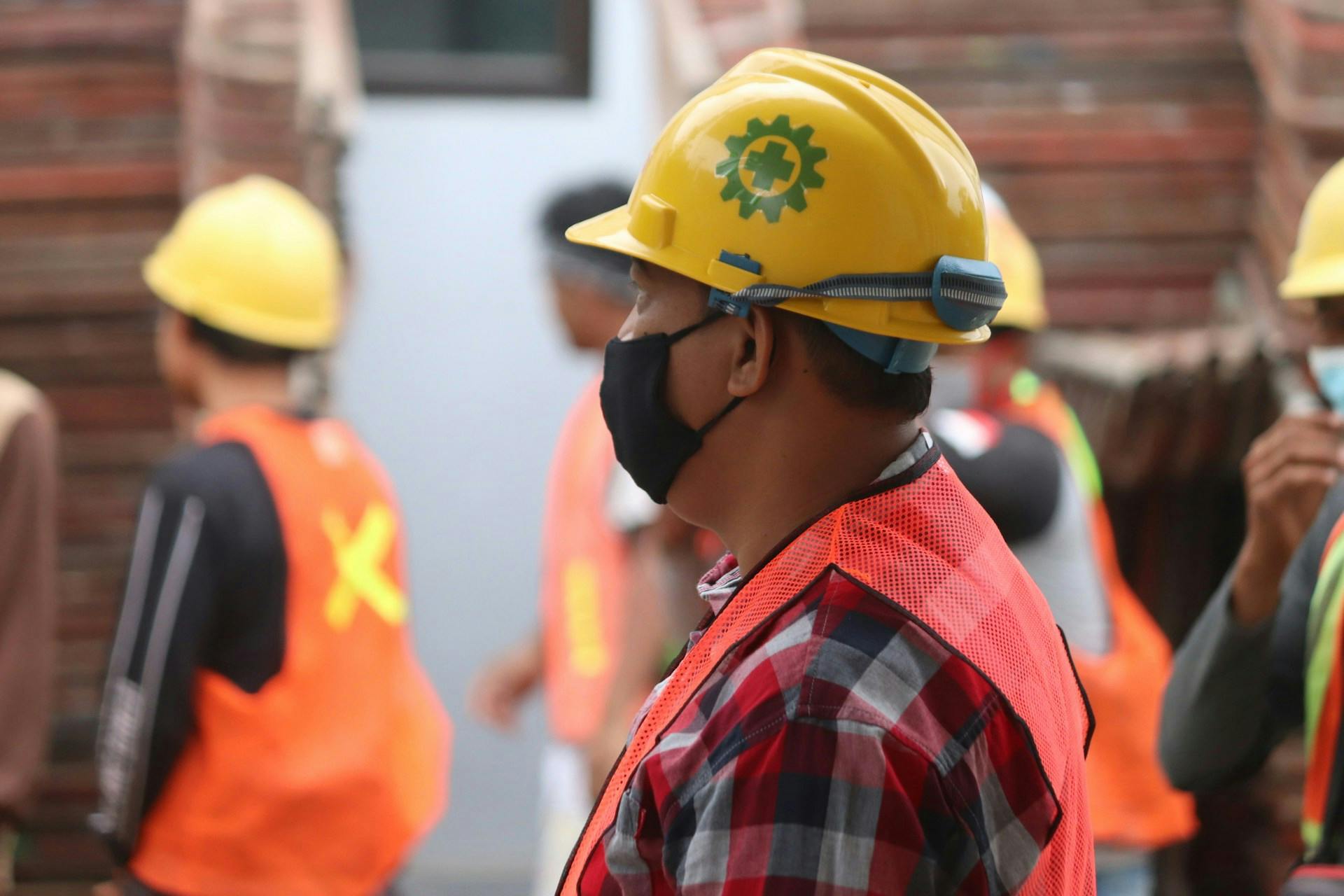
Many organizations approach workplace safety as a compliance exercise—following OSHA regulations, conducting required training, and avoiding penalties. But true safety culture runs deeper.
According to the CDC's National Institute for Occupational Safety and Health, safety culture includes "the shared values, beliefs, norms, and behavioral patterns that determine the ways in which your organization's management and employees think about and act toward safety."
Organizations with strong safety cultures integrate safety into everyday operations by following essential safety rules. Safety discussions start meetings, workers stop unsafe work without fear, and leaders regularly walk the floor to reinforce safe behaviors through their visible commitment.
The Business Case for a Strong Workplace Safety Culture
Building a robust workplace safety culture makes good business sense. Organizations focused on safety see substantial benefits that impact their bottom line while creating a better work environment.
Tangible ROI: The Measurable Impact
When safety becomes core to your organization, the financial benefits quickly appear:
- Reduced Workplace Incidents: Companies with strong safety programs have up to 50% lower injury rates according to the National Safety Council. This directly translates to fewer disruptions and less lost time.
- Lower Workers' Compensation Costs: Fewer injuries mean fewer claims and lower insurance premiums. You can redirect these savings toward growth rather than paying for preventable incidents.
- Reduced Absenteeism: When people feel safe at work, they miss fewer work days due to injuries or stress, creating a more stable workforce and reducing costs for replacements or overtime.
- Equipment Longevity: Safety protocols often include proper maintenance, extending equipment life and delaying replacement costs.
- Decreased Insurance Premiums: Insurance carriers reward strong safety records with lower premiums.
Intangible Benefits of a Strong Workplace Safety Culture
The non-financial benefits of a strong workplace safety culture matter just as much:
- Enhanced Employee Morale: When workers know their wellbeing matters, it builds trust and improves workplace satisfaction.
- Improved Retention: Safety-focused organizations typically see lower turnover. People stick with companies that genuinely care about their welfare.
- Increased Productivity: 79% of workers report feeling more productive in workplaces with strong safety cultures. When not worried about hazards, people focus better on their work.
- Strengthened Company Reputation: A strong safety record enhances your reputation with customers, potential employees, regulators, and the community.
- Higher Employee Engagement: Involving employees in safety initiatives encourages ownership and connection to the organization's goals.
Workplace Safety Culture as a Business Performance Driver
The most compelling evidence comes from organizations that made safety their cornerstone.
Alcoa's transformation under CEO Paul O'Neill stands out. When O'Neill took over the aluminum company in 1987, he shocked Wall Street by announcing his top priority wouldn't be profits—it would be worker safety.
O'Neill made safety the focal point of every leadership meeting and gave any employee power to report safety concerns directly to top management. The results? Within a year, Alcoa's lost workday rate from injuries fell by 50%. Even more surprising, during O'Neill's tenure, Alcoa's annual net income increased five-fold, and its market value grew by $27 billion.
This shows how a strong workplace safety culture doesn't just coexist with business performance—it drives it. When organizations prioritize safety, they build discipline, communication systems, and leadership practices that benefit every aspect of operations.
Leadership's Critical Role in Workplace Safety Culture
When it comes to workplace safety culture, the tone is set from the top. Leaders at all levels shape and maintain the safety culture that protects everyone. Leadership commitment forms the foundation of strong workplace safety cultures—without it, even comprehensive safety programs fall short.
Setting the Tone from the Top
Executive leadership shows their commitment to safety through actions, not just words:
- Allocating enough budget and resources for safety improvements
- Regularly appearing on the plant floor for safety conversations
- Putting employee safety above production goals or deadlines
- Making safety a priority in every meeting
When executives visibly value safety, employees understand it's a core value, not just policy. This commitment must be genuine—employees quickly spot when safety gets mere lip service.
DuPont's "Safety First" philosophy dates back to the company's founders and has remained a core value for over 200 years. DuPont executives regularly join safety audits and reviews, showing that safety remains a priority regardless of production pressures.
Middle Management: The Link in Workplace Safety Culture
While executive commitment matters, middle managers serve as the important link that turns high-level safety commitment into daily reality. They act as safety ambassadors who:
- Put safety policies and procedures into practice, ensuring they are relevant to each specific team
- Ensure workers have proper training and equipment, providing ongoing learning opportunities
- Address safety concerns quickly, fostering an open-door policy for immediate reporting
- Communicate safety expectations clearly, ensuring every worker knows the standards
- Reinforce safe behaviors through recognition and coaching, building a culture of accountability
Middle managers balance productivity targets with safety requirements. When properly supported, they become the living embodiment of safety values, connecting corporate safety policies with frontline practices.
The most successful organizations recognize that workplace safety culture requires intentional leadership at all levels, with executives setting the vision, middle managers implementing it daily, and everyone demonstrating safety commitment through their actions.
Communication Strategies to Enhance Workplace Safety Culture Among Non-Desk Workers
In industrial and service environments, communication can be one of the biggest challenges to building an effective workplace safety culture. The reality is stark: 83% of non-desk workers don't have access to company email, and they spend over 90% of their time doing their jobs, leaving minimal opportunity to check traditional communication channels.
The Unique Challenges of Non-Desk Communication
Non-desk workers face distinct communication barriers that desk-based employees don't encounter:
- Limited or no computer access during the workday
- Noisy work environments that make verbal communication difficult
- Multiple shifts and scattered locations
- Language barriers in diverse workforces
- Time constraints with minimal breaks
These challenges require a complete rethink of safety communication. What works in an office environment often fails completely on the shop floor, construction site, or in the field. Understanding these communication barriers for deskless workers is essential for developing effective safety communication strategies.
Multi-Channel Communication Frameworks That Enhance Workplace Safety Culture
The most successful organizations implement effective strategies for non-desk communication by using multi-channel communication frameworks that combine technology with in-person interactions. This approach ensures safety information reaches everyone, regardless of their role or location, which is crucial for communicating safety protocols.
A well-designed framework typically includes various communication tools for deskless workers, such as:
- Face-to-face toolbox talks and safety meetings
- Visual communication through strategically placed signage and digital displays
- Mobile-friendly digital solutions like SMS that don't require company email or an internet connection
- Printed materials in common areas for those without digital access
Text messaging platforms like Yourco have emerged as particularly effective tools for non-desk worker communication due to the numerous benefits of SMS communication. This platforms offer several advantages:
- No app download required—messages arrive via standard SMS
- Near-instant delivery of safety alerts through automated text messaging
- Ability to reach workers across multiple locations simultaneously
- Two-way communication capabilities
- Document sharing for safety procedures and training materials
- Multilingual support to overcome language barriers
These platforms serve as an effective emergency notification system, ensuring important information reaches workers promptly. Plus, the high read rates of text messages (98%+) make them significantly more effective than emails, which often go unread by field workers.
Two-Way Communication: Creating Feedback Loops
Perhaps the most important aspect of non-desk worker communication is establishing effective feedback loops. Workers on the front lines often spot potential hazards first, but without easy ways to report concerns, this valuable information gets lost.
Creating strong feedback loops requires:
- Simple reporting mechanisms accessible from the field
- Anonymous reporting options to encourage candid feedback
- Quick response times to show workers their input matters
- Regular follow-up on reported issues
- Recognition for workers who identify safety concerns
Implementing effective internal communication strategies is important to facilitate these feedback loops. When designing your communication approach, remember that different messages may need different channels.
Emergency alerts might work best via text message, while detailed safety procedures might need a combination of in-person training and accessible digital resources. The key is matching the medium to the message while ensuring no employee is left uninformed.
Measuring Your Current Workplace Safety Culture
Before improving your workplace safety culture, you need to understand where you stand now. A thorough assessment provides the foundation for targeted improvements and helps track progress over time.
Assessment Tools and Methodologies
Several validated tools can help evaluate your organization's safety culture:
- Safety Culture Surveys: These standardized questionnaires measure employee perceptions about safety across multiple dimensions, offering insight into how safety is perceived throughout the workforce.
- Safety Climate Assessments: These tools focus specifically on employee perceptions of safety policies, procedures, and practices within the organization, helping pinpoint areas of concern in your safety system.
- Safety Audits and Inspections: Structured evaluations of your physical environment, documentation, and safety practices provide objective data about compliance with safety standards, highlighting potential risks or areas for improvement.
For best results, use a combination of these approaches to get both quantitative data and qualitative insights. This comprehensive approach allows for more effective safety culture assessments and informed decision-making.
Leading vs. Lagging Safety Indicators
A comprehensive assessment should include both leading and lagging indicators:
Leading Indicators are predictive, forward-looking measures that can help prevent incidents before they occur:
- Near-miss reporting rates
- Safety training completion percentages
- Percentage of corrected hazards identified during inspections
- Employee participation in safety meetings
- Number of safety suggestions submitted
Lagging Indicators are reactive measures that track safety outcomes after they've occurred:
- Injury rates (TRIR - Total Recordable Incident Rate)
- Workers' compensation costs
- Lost workday cases
- Property damage incidents
- OSHA violations and fines
While lagging indicators have traditionally dominated safety metrics, leading indicators provide early warning signs of potential problems. A balanced scorecard approach gives you the most complete view of your workplace safety culture.
Employee Perception Surveys: What to Ask and How to Interpret
Employee perception surveys help understand how your workforce views safety practices. When designing these surveys, focus on these areas:
- Leadership commitment: Do employees believe management prioritizes safety over production?
- Communication: Are safety concerns openly discussed without fear of retaliation?
- Employee involvement: Do workers feel empowered to participate in safety initiatives?
- Risk perception: How do employees view workplace hazards and safety procedures?
- Trust: Do employees trust that management will address safety concerns?
When interpreting survey results:
- Look for patterns across departments or job roles
- Pay attention to both positive findings and areas for improvement
- Compare responses to industry benchmarks when available
- Consider the response rate (low participation may itself indicate safety culture issues)
- Track changes over time to measure the impact of interventions
Remember that survey data reflects perceptions, which may differ from reality but are equally important for understanding your workplace safety culture.
Safety Culture Maturity Models
Safety culture maturity models provide a framework for assessing your organization's developmental stage. Most models identify five progressive levels:
- Pathological: Safety is seen as a problem caused by workers. The main drivers are business and avoiding authority.
- Reactive: Safety is taken seriously, but only after incidents occur. There's little preventive action.
- Compliant: Safety systems are in place to manage hazards. Safety is primarily driven by management and imposed rather than embraced.
- Proactive: Workers and management have a shared belief in the importance of safety. They take a proactive approach to identifying and addressing risks.
- Generative: Safety is integral to the business. Organizations at this level exhibit informed vigilance and are characterized by chronic unease that prevents complacency.
Identifying your current maturity level helps you develop targeted strategies to advance to the next stage and track your progress over time.
The results from your safety culture assessment aren't just data points—they're the foundation for strategic improvement. They help you identify strengths to build on and specific areas needing attention, ensuring your safety initiatives focus where they'll have the greatest impact.
Yourco can help with gathering this information quickly and easily using built-in surveys and polls.
Creating a Workplace Safety Culture Roadmap
Building a strong workplace safety culture takes careful planning, consistent execution, and ongoing commitment. To transform your organization's approach to safety, you need a clear roadmap from where you are to where you want to be.
Step-by-Step Implementation Planning
The first step in your safety culture transformation is developing a thorough implementation plan that:
- Begins with a comprehensive assessment of your current safety culture through surveys, focus groups, and safety metrics analysis
- Defines your vision for safety and how it aligns with your organization's overall objectives
- Identifies stakeholders and forms a dedicated safety culture team
- Develops specific, measurable goals for your transformation
- Creates detailed action plans for each phase of implementation
Your implementation plan should address all aspects of workplace safety culture, including leadership behaviors, communication processes, training programs, and recognition systems. Involve representatives from all levels of the organization in this planning process to gain diverse perspectives and build buy-in from the start.
Setting Realistic Timelines for Cultural Change
One common mistake is underestimating how long it takes to transform safety culture. Cultural change isn't quick—it needs sustained effort over time.
A realistic timeline for meaningful safety culture transformation typically spans 18-24 months. This gives enough time for new behaviors to become habits and for the organization to overcome resistance to change.
Here's what a sample 18-month safety culture transformation timeline might look like:
Months 1-3: Assessment and Planning
- Conduct baseline safety culture assessment
- Develop vision and strategy
- Form safety culture steering committee
- Identify and train safety champions
Months 4-6: Early Implementation
- Launch communication campaign
- Begin leadership safety training
- Implement near-miss reporting system
- Revise safety policies and procedures
Months 7-12: Full Implementation
- Roll out employee safety training
- Implement safety observation program
- Begin regular safety walkarounds by leadership
- Launch recognition program for safety contributions
Months 13-18: Sustainability and Measurement
- Conduct follow-up safety culture assessment
- Refine programs based on feedback
- Develop sustainability plan
- Celebrate successes and share lessons learned
While you need a structured timeline, stay flexible and adapt your approach based on feedback and results.
Resource Allocation for Safety Initiatives
For your workplace safety culture transformation to succeed, allocate adequate resources across these areas:
Budget: Set aside funding for:
- Training programs and materials
- Communication campaigns
- Safety recognition and incentives
- External consultants or facilitators (if needed)
- Technology solutions for reporting and tracking
- Time for employees to participate in safety activities
Personnel: Consider who will:
- Lead the overall transformation effort
- Serve on safety committees
- Act as safety champions within departments
- Provide training and coaching
- Analyze safety data and track progress
Technology: Invest in tools that support your safety culture, such as:
- Safety reporting systems that make it easy to report hazards and near-misses
- Data analytics platforms to identify trends and opportunities
- Communication platforms that reach all employees, including non-desk workers
- Learning management systems for safety training
When allocating resources, remember that leaders must show that safety is a priority. Leaders must commit to creating and maintaining a culture of safety; this commitment is just as important as the time and resources devoted to revenue and financial stability, system integration, and productivity.
Remember that building a workplace safety culture isn't a linear process. You'll likely face setbacks and resistance. The key is learning from these challenges and continuously refining your approach.
Industry-Specific Considerations for Workplace Safety Culture
Different industries face unique safety challenges that require tailored approaches to building and maintaining a strong workplace safety culture. Let's explore how safety culture varies across several sectors.
Manufacturing Safety Culture Essentials
In manufacturing environments, safety culture must address the specific hazards of production facilities:
- Comprehensive hazard identification: Manufacturing settings contain numerous mechanical, electrical, and chemical hazards that require systematic identification processes. Regular workplace safety inspections and audits help spot potential dangers before they cause incidents.
- Machine safety protocols: Clear lockout/tagout procedures, machine guarding requirements, and equipment-specific training are essential. These protocols should be standardized and regularly reviewed to ensure they remain effective as equipment and processes evolve.
- Process standardization: Manufacturing safety depends heavily on consistent processes. Developing comprehensive written safety policies, establishing clear procedures for high-risk tasks, and creating checklists for common operations helps ensure safety procedures are followed consistently across shifts and teams.
- Operator involvement: Successful manufacturing safety cultures actively engage machine operators in safety committees and decision-making processes, utilizing effective manufacturing employee engagement strategies. Their practical knowledge helps identify potential hazards and develop effective safety measures.
- Incident reporting process: Implement a clear and simple incident reporting process. This ensures workers can easily report accidents and near-misses, while tools that timestamp and store records provide accountability and valuable insights for improving safety.
Healthcare Safety Culture Requirements
Healthcare settings present unique challenges with patient safety being intertwined with worker safety:
- Patient safety integration: Healthcare safety culture must integrate worker safety with patient safety concerns. Safety procedures should address both simultaneously, recognizing how they impact each other.
- Infection control emphasis: Healthcare safety culture places significant emphasis on infection prevention protocols. This includes proper use of personal protective equipment (PPE), hand hygiene practices, and strict adherence to isolation precautions.
- Reporting systems: Non-punitive reporting systems are especially important in healthcare. The focus should be on learning and improvement rather than punishment when incidents occur. This encourages staff to report near-misses and adverse events that might otherwise go unreported.
- Interdisciplinary approach: Healthcare safety requires coordination across various disciplines. Safety committees should include representatives from different departments to address the complex, interconnected nature of healthcare delivery.
Construction Industry Safety Culture Challenges
The construction industry faces some of the most significant safety challenges due to the dynamic nature of work environments:
- Temporary worksite management: With constantly changing work environments, construction safety culture must emphasize adaptability and frequent safety assessments. Site-specific hazard assessments should happen before work begins at each new location.
- Subcontractor management: Construction projects typically involve multiple subcontractors working simultaneously. Establishing safety requirements for all contractors, including them in safety training and meetings, and holding them accountable to the same safety standards as employees helps maintain a consistent safety culture across the project.
- High-risk operations: Construction involves numerous high-risk activities including working at heights, excavation, and heavy equipment operation. Safety protocols must address these specific risks with clear guidelines and proper training.
- Innovative safety programs: Many construction companies have developed innovative approaches to workplace safety culture. For example, construction company Skanska implemented a "Stretch and Flex" program where crews gather each morning to do light stretching exercises. This daily touchpoint allows supervisors to discuss the day's safety considerations and for workers to voice any concerns.
- Technology adoption: Forward-thinking construction companies are using technology to enhance safety. For instance, Bechtel uses drones for site inspections, reducing the need for workers to access dangerous areas.
- Incident reporting - Once again it is important to have a clear and simple incident reporting process where workers can report accidents and near-misses. Using digital tools like Yourco can help streamline this process.
Make Workplace Safety a Competitive Advantage
A strong safety culture doesn’t happen by accident — it’s built through leadership, consistency, and clear communication. For organizations with non-desk workers, that communication must be both immediate and accessible. Yourco makes that possible.
More than just a text-messaging tool, Yourco serves as a centralized hub for safety documentation, incident reports, and insurance claims. When something goes wrong — an injury, an unsafe condition, or property damage — employees can snap a photo and send it directly via SMS to the company’s dedicated Yourco number. That message is timestamped, stored, and instantly integrated into the company’s internal records.
This matters. Why?
- No waiting until the end of the shift to file a report.
- No forgotten details.
- No paperwork bottlenecks.
- No gaps in documentation that could jeopardize an insurance claim or legal defense.
Yourco ensures accurate, real-time incident capture, providing a digital paper trail that protects your people and your business. Safety managers or HR can immediately follow up to gather additional context or initiate next steps, all within a secure, encrypted, role-based system designed for compliance and privacy
And because it’s all done through SMS, employees don’t need to download an app, remember a password, or even have mobile data. It works on the tools they already have; their phones.
Try Yourco for free today or schedule a demo and see the difference the right workplace communication solution can make in your company.