Safety Improvement Plan for Non-Desk Workers: A Must-Have Template
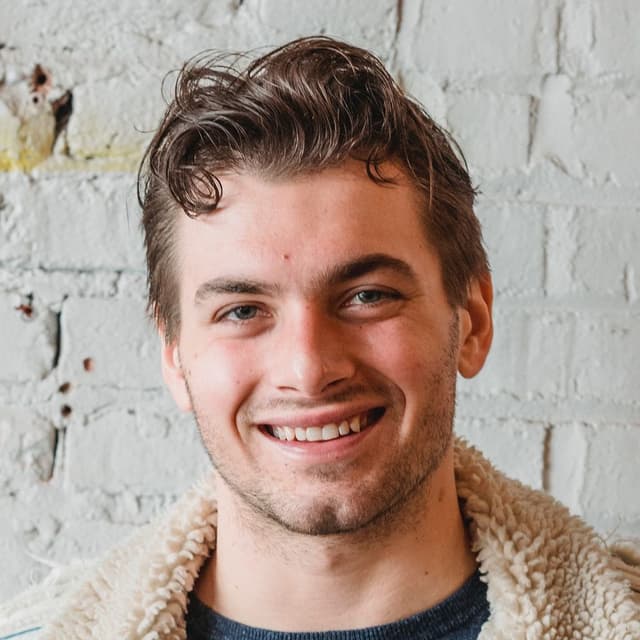
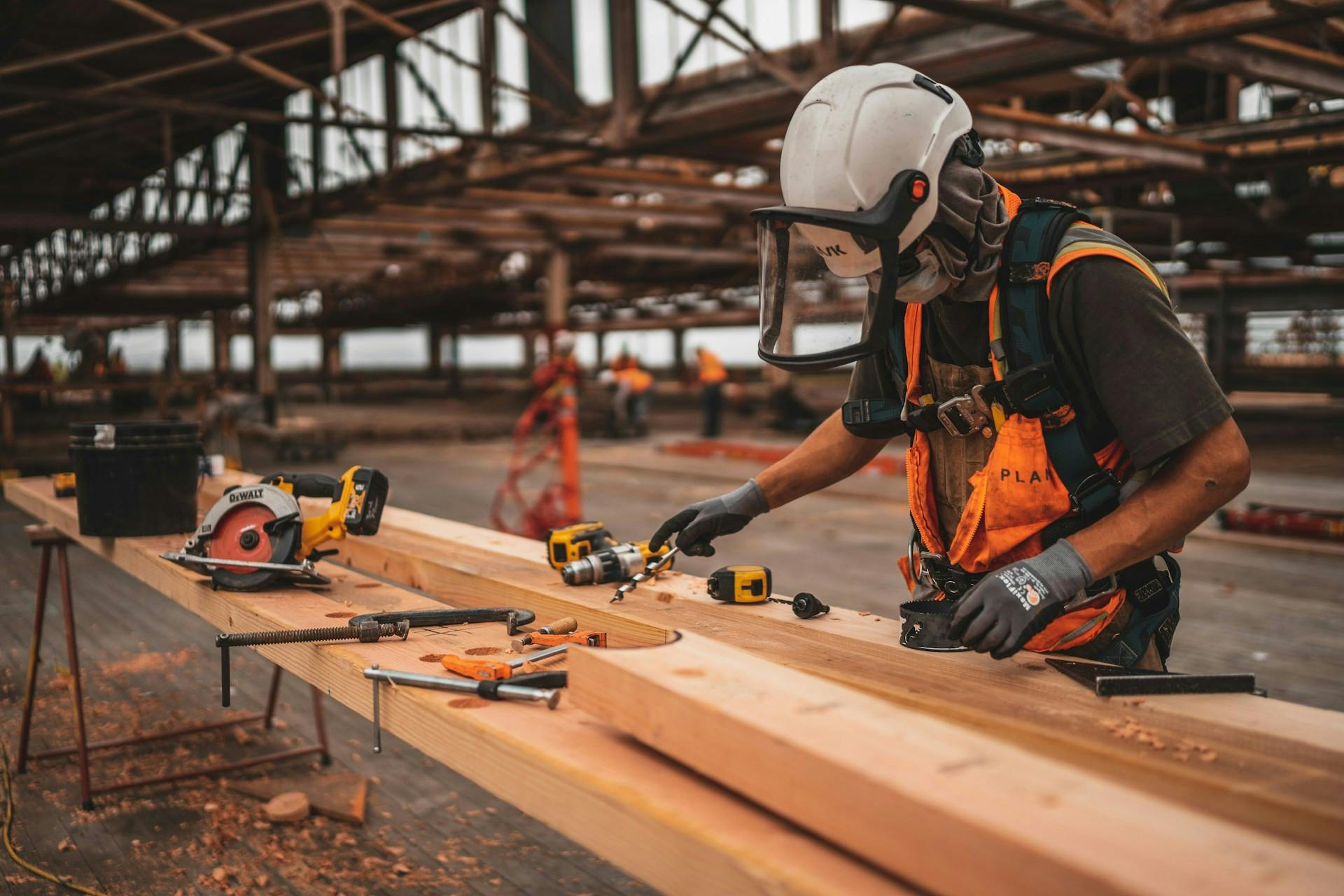
A safety improvement plan identifies, assesses, and mitigates workplace risks to protect employees from harm. Organizations employing non-desk workers need comprehensive safety planning to address the high risks of injuries and fatalities their frontline workers face. Effective safety measures create safer environments while improving morale and operational efficiency.
According to the U.S. Bureau of Labor Statistics, 2022 saw an increase in worker fatalities and non-fatal injuries, highlighting ongoing safety challenges in these sectors. Beyond moral obligations, safety planning helps companies meet OSHA regulations while improving employee retention.
Assessing Your Current Safety Environment
Before developing a safety improvement plan, you need to thoroughly understand your current safety landscape. A comprehensive assessment creates a baseline that helps you identify existing gaps, measure future progress, and target your resources where they'll have the most impact.
Conducting a Comprehensive Safety Audit
Start with thorough workplace inspections across all facilities, work areas, and job sites. As part of your safety improvement plan, your safety audit should include:
- Physical examination of equipment, tools, and machinery to identify wear, defects, or hazards
- Review of existing safety protocols and documentation
- Evaluation of current PPE usage and availability, checking for compliance and proper fit
- Assessment of safety signage and communication systems, ensuring clarity and visibility
- Observation of actual work practices versus documented procedures to identify gaps or training needs
Safety audits work best when they involve cross-functional teams. Include safety professionals, supervisors, and most importantly, frontline workers who know the day-to-day operations and potential hazards better than anyone.
Analyzing Safety Performance Data
Historical data provides valuable insights into your organization's safety performance trends. Collect and analyze the following depending on availability:
- Incident reports and accident investigations to understand root causes and contributing factors
- Near-miss reports to identify potential hazards before they result in injuries
- Workers' compensation claims to track cost trends and common injury types
- Past compliance inspection results to ensure ongoing adherence to regulations
- Safety training records to assess participation and effectiveness
- Previous audit findings to pinpoint areas needing improvement
Look for patterns in this data—recurring incidents in specific locations, times, or job functions may point to systemic issues requiring attention. Don't just focus on what went wrong; also analyze what's working well so you can replicate successful practices.
Identifying Critical Risk Areas
After gathering information through audits and data analysis, prioritize your findings to identify the most important risk areas for your safety improvement plan. Consider:
- Frequency and severity of past incidents
- Potential for catastrophic outcomes
- Number of workers exposed to the hazard
- Regulatory compliance requirements
- Feasibility of risk reduction measures
Engage your frontline workers in this prioritization process. Their practical experience often provides insights that might not be evident from data alone. Ask them about "near misses" or safety concerns they've observed but perhaps haven't formally reported.
Workers who perform tasks daily understand the nuances of their jobs better than anyone else. Create an environment where they feel comfortable sharing concerns without fear of reprisal. This could involve anonymous reporting systems, safety suggestion programs, or direct conversations.
A thorough assessment of your current safety environment builds a solid foundation for a targeted safety improvement plan that addresses real issues rather than perceived problems.
This assessment isn't a one-time activity—as you implement improvements, continue to monitor and reassess to ensure your safety improvement plan evolves with your changing workplace.
Developing Your Safety Improvement Plan
Creating an effective safety improvement plan reduces incidents and builds a sustainable safety culture that resonates with your non-desk workforce.
Establishing Clear Objectives and Goals for Your Safety Improvement Plan
The foundation of any effective safety improvement plan starts with establishing clear, measurable objectives. For non-desk environments, implement SMART goals:
- Specific: Target particular hazards or behaviors relevant to your operation
- Measurable: Establish concrete metrics to track progress
- Achievable: Set realistic targets that motivate rather than discourage
- Relevant: Align with the actual risks your workforce faces
- Time-bound: Create deadlines to maintain momentum
For example, instead of a vague goal like "improve safety," set a target such as "reduce slip and fall incidents by 20% within six months through enhanced housekeeping procedures and worker education."
Consider separating your goals into leading indicators (preventive measures like training completion rates) and lagging indicators (outcome measures like incident rates) to gain a comprehensive view of your safety performance.
Creating an Effective Safety Governance Structure for Your Safety Improvement Plan
A robust governance structure ensures accountability and sustained focus on your safety objectives. For non-desk environments, this structure should include:
- Cross-functional representation: Include members from operations, maintenance, quality, and frontline workers to capture diverse perspectives
- Clear roles and responsibilities: Define who is responsible for implementing, monitoring, and reporting on safety initiatives
- Regular meeting cadence: Establish a consistent schedule for reviewing progress and addressing emerging issues
- Direct reporting line to leadership: Ensure safety concerns have a clear path to decision-makers
In manufacturing environments, successful governance models often have each department nominate a safety champion who participates in a site-wide safety committee while maintaining departmental responsibilities.
The governance structure must reflect your operational reality. For distributed workforces like field service teams, consider regional safety coordinators who can address location-specific challenges while maintaining alignment with company-wide safety improvement plans.
Developing Action-Oriented Safety Initiatives for Your Safety Improvement Plan
With objectives and governance in place, you need specific initiatives that drive real change. Effective safety initiatives for non-desk environments should be:
- Practical and relevant: Address the actual conditions workers face daily
- Easy to implement: Design initiatives that integrate into existing workflows
- Measurable: Include clear metrics to track implementation and effectiveness
- Well-resourced: Provide necessary tools, time, and training
Examples of effective initiatives include:
- Job-specific hazard identification programs where workers actively participate in identifying and mitigating risks
- Peer observation systems that encourage workers to provide feedback on safe and at-risk behaviors
- Near-miss reporting processes that make it easy for workers to flag potential incidents
- Task-specific training modules delivered in short, frequent sessions rather than lengthy annual reviews
Implementing these effective communication practices increases knowledge retention while minimizing time away from productive work.
Throughout this process, leadership commitment is important. Ensure top management is visibly committed to safety improvements through regular site walks, participation in safety meetings, and allocation of necessary resources. When leaders demonstrate that safety is a priority, workers follow suit.
Remember that your safety improvement plan should be a living document. Review it regularly, adjust based on results and feedback, and continuously seek new ways to enhance safety for your non-desk workforce.
Implementation Strategies for Non-Desk Workforces in Your Safety Improvement Plan
Implementing safety improvement plans for distributed, non-desk workforces presents unique communication challenges that require specialized approaches. Unlike office settings where communication channels are readily available, frontline work environments demand more creative and targeted strategies to ensure safety information reaches everyone effectively.
Effective Safety Communication Tactics
The traditional communication tools that work well in office settings often fall short with distributed workforces. One of the biggest challenges is delayed information dissemination, where important safety updates may reach workers days or even weeks after they're issued.
Additionally, inconsistent messaging can occur when relying on word-of-mouth or bulletin boards, leading to misunderstandings and varying levels of compliance.
Developing effective communication strategies for deskless workers is essential to address these issues. To overcome these barriers in your safety improvement plan, consider implementing the following:
- SMS/text messaging for urgent safety updates, which ensures rapid dissemination of important information
- Digital signage in common areas displaying up-to-date safety information
- Visual communication tools like infographics and videos that enhance understanding across language barriers
Training and Competency Development
Non-desk environments require training approaches that align with how frontline workers learn best. Abstract concepts and lengthy presentations typically don't translate well to practical application in the field. Training should be engaging, accessible, and directly applicable to daily tasks.
Effective training strategies for your safety improvement plan include:
- Hands-on instruction for proper use of PPE, safe operation of tools and machinery, and hazard identification
- Microlearning approaches that break down complex safety topics into digestible chunks workers can quickly absorb
- Interactive training modules that workers can access during downtime
- Real-world scenario-based drills that reinforce best practices
These approaches increase knowledge retention while minimizing time away from productive work.
Fostering Employee Engagement and Ownership
When workers feel personally invested in safety outcomes, compliance increases dramatically. The challenge with distributed workforces is creating this sense of ownership without constant supervision.
Strategies to encourage engagement in your safety improvement plan include utilizing effective employee communication strategies such as:
- Regular safety huddles at the beginning of shifts to discuss relevant safety topics
- Peer-to-peer safety observation programs where workers look out for each other
- Anonymous reporting tools that allow workers to report concerns without fear of reprisal
- Recognition programs that acknowledge and reward safe behaviors and proactive safety contributions
Bill Woods, Director of Safety at American Welding & Gas, emphasizes several approaches: "Management by Walking Around; Communicating safety expectations; Leading by example; Gentle reminders; Accountability."
Implementing these targeted strategies can lead to successful non-desk employee communication, overcoming the unique challenges of non-desk environments and creating a robust safety culture even among distributed workforces. The right approaches differ from traditional office settings, and adapting your safety improvement plan accordingly makes all the difference.
Leveraging Technology for Non-Desk Worker Safety
Technology has become an invaluable asset in protecting non-desk workers across various industries. Implementing the right digital tools within your safety improvement plan addresses many of the unique challenges faced by frontline employees while enhancing overall safety outcomes.
Mobile Tools for Real-Time Reporting and Communication
Digital technology offers powerful capabilities for instant safety communication with workers in the field:
- Simple reporting platforms enable employees to document hazards or near-misses immediately, rather than waiting until they return to an office
- SMS-based communications provide incredible reach, with a 98% read rate compared to other communication channels, making them highly effective for alerting employees
- Push notifications can deliver important safety alerts directly to workers' devices during emergencies. Implementing an emergency notification system or mass notification systems ensures rapid dissemination of critical information to all employees
Text-based tools work best when they're intuitive and integrated into daily workflows. The most successful implementations require minimal additional steps and provide clear value to workers, not just management.
Overcoming Language Barriers with Translation Technology
Language differences can create serious safety risks when important information isn't clearly understood. Implementing multilingual emergency alert systems and AI-powered translation tools can convert safety instructions and emergency alerts into multiple languages simultaneously.
These technologies are vital for overcoming language barriers on job sites and ensuring all workers receive critical safety information.
- AI-powered translation tools can convert safety instructions and emergency alerts into multiple languages simultaneously
- Real-time translation capabilities enable effective communication during safety briefings and training sessions
- Multilingual interfaces ensure all workers can access important safety information
Los Angeles County successfully used AI translation tools to provide real-time translations of wildfire evacuation instructions in over 60 languages, ensuring important safety information reached non-English speaking residents effectively during emergencies.
When implementing translation technology in your safety improvement plan, it's important to maintain human oversight, especially for safety-critical communications. The best approach combines AI translation with review by bilingual staff for technical terminology and important instructions.
While these technological solutions offer tremendous benefits, they should supplement, not replace, face-to-face safety interactions. The most effective safety programs use technology to enhance human connections, not substitute for them.
Digital tools work best when integrated into a comprehensive safety culture that values personal communication and demonstrates genuine concern for worker wellbeing.
Measuring Success and Continuous Improvement
To ensure your safety improvement plan delivers meaningful results, you need to establish clear metrics and implement a process for ongoing evaluation and refinement. The right approach combines both reactive and proactive measurements to give you a complete picture of your safety performance.
Tracking Leading and Lagging Indicators
Effective measurement requires balancing two types of metrics:
Lagging Indicators measure outcomes after incidents occur:
- Total Recordable Incident Rate (TRIR): Calculate by multiplying the number of recordable incidents by 200,000, then dividing by total hours worked. This standardized OSHA metric allows you to benchmark against industry averages.
- Lost Time Injury Frequency Rate (LTIFR): Measures incidents resulting in lost workdays, helping you understand how injuries impact productivity.
- Days Away, Restricted, or Transferred (DART) Rate: Focuses on more severe injuries that prevent normal work duties.
While these metrics are important for compliance and tracking historical performance, they're reactive by nature. That's why you also need Leading Indicators as they help predict and prevent future incidents:
- Near-miss reporting rate: A healthy safety culture shows high rates of near-miss reporting, indicating employees feel comfortable highlighting potential hazards.
- Safety training completion percentages: Track how many employees have completed required training programs.
- Hazard identification and correction rates: Monitor how quickly identified hazards are addressed and resolved.
A balanced scorecard approach combining both types of indicators gives you the most comprehensive view of your safety program's effectiveness.
Building a Sustainable Safety Culture
Metrics and reviews are only effective when embedded within a strong safety culture:
- Celebrate successes – Recognize and reward positive safety behaviors and achievements.
- Communicate consistently – Share both metrics and improvement actions with your entire workforce regularly.
- Empower employees – Give workers authority to stop work when unsafe conditions exist and involve them in developing solutions.
- Integrate safety into everyday operations – Safety shouldn't be a separate program but woven into all aspects of your business.
Sustainable improvement requires shifting from a compliance mindset to one that views safety as a core value. When employees at all levels understand not just what to measure but why it matters, your safety culture becomes self-reinforcing.
Remember that continuous improvement is exactly that—continuous. Your measurements and methods should evolve as your safety improvement plan matures and new challenges emerge. This disciplined approach to measurement and improvement creates a progressively safer environment for your non-desk workforce.
Addressing Industry-Specific Safety Challenges
When developing safety improvement plans for non-desk workers, it's important to recognize that different industries face unique hazards requiring tailored approaches. A one-size-fits-all safety protocol often fails to address the specific risks inherent to construction, manufacturing, transportation, or field service operations.
Construction and Field Services Safety Considerations
Construction and field service workers face some of the most varied safety environments. These industries require special attention to:
- Fall protection systems specific to various heights and surfaces
- Site-specific hazard assessments that change as construction progresses
- Equipment safety protocols that evolve with different project phases
- Weather-related safety precautions, especially for outdoor operations
According to the U.S. Bureau of Labor Statistics, construction consistently reports higher rates of worker fatalities compared to other industries. To combat this, some forward-thinking construction companies now utilize drones for site inspections and mobile checklists for safety training, resulting in significant reductions in height-related incidents.
For field service workers who often work alone or in small teams, safety improvement plans should incorporate check-in procedures and emergency response protocols tailored to remote locations.
Manufacturing and Industrial Environments
Manufacturing settings present different challenges that require specific safety measures:
- Machine-specific lockout/tagout procedures (rather than generic ones) tailored to each piece of equipment
- Customized ergonomic interventions based on detailed workstation analysis to prevent strain injuries
- Noise protection protocols designed for specific equipment and noise levels in different areas
- Chemical safety procedures customized for the substances used in production to ensure proper handling and disposal
Safety improvement plans should also address the unique challenges of shift work, as irregular schedules can impact alertness and increase the risk of accidents. To tackle this, strategies could include rotating shifts, regular breaks, and increased focus on worker wellness to maintain vigilance and safety.
Transportation and Logistics Safety Planning
Transportation and logistics workers face distinct safety challenges that require specialized approaches:
- Driver-specific fatigue management programs
- Vehicle-specific maintenance and pre-trip inspection protocols
- Loading/unloading procedures customized to cargo types
- Route-specific hazard identification and mitigation strategies
For trucking companies, effective safety improvement plans often incorporate telematic systems and mobile simulation training that present various driving conditions and scenarios. These technologies have shown up to 55% improvement in safety awareness compared to traditional safety training methods.
Transportation safety improvement plans must also address the unique challenge of communication with mobile workers who may traverse multiple jurisdictions with varying regulations and hazards.
When developing industry-specific safety improvement plans, the most successful approaches involve:
- Consulting with workers who perform the specific tasks to identify nuanced hazards
- Creating visual safety materials that address industry-specific scenarios
- Developing industry-benchmarked safety metrics to track progress
- Building in flexibility to adapt to changing conditions and regulations
Tailoring safety improvement plans to address the specific hazards and operational realities of different frontline industries creates more effective programs that workers recognize as relevant to their daily challenges, ultimately driving higher engagement and better safety outcomes.
Overcoming Common Implementation Challenges
Implementing safety improvement plans for non-desk workers comes with unique obstacles that can derail even the best-designed initiatives. Anticipating these challenges and preparing for them proactively significantly increases your chances of success.
Addressing Resistance to Change
Resistance to new safety protocols is a natural human response, especially among experienced workers who may feel their expertise is being questioned. To overcome this:
- Involve workers early in the planning process to gain buy-in and valuable frontline insights. Their input can highlight potential challenges and improve the plan's effectiveness
- Clearly communicate the "why" behind new safety measures, not just the "what" or "how." Understanding the reasoning behind the changes fosters trust and acceptance
- Start with small, achievable changes to build momentum before tackling larger initiatives. This approach helps workers experience success and feel more confident in adopting new protocols
- Identify and support informal leaders who can champion safety improvements among their peers, making adoption smoother
Maintaining Consistency Across Multiple Locations
For organizations with distributed workforces, ensuring uniform safety standards can be particularly challenging:
- Develop standardized safety protocols within your safety improvement plan while allowing flexibility for site-specific adaptations, ensuring relevance to each unique location
- Implement digital solutions that provide real-time visibility into safety compliance across all locations, helping monitor adherence to safety protocols at any time
- Create a central safety resource hub that all locations can access for the latest information, including updated SOPs, training materials, and compliance requirements
- Establish a network of local safety champions who are responsible for consistent implementation and monitoring, providing support to workers and ensuring safety standards are met consistently across the organization
Sustaining Long-Term Engagement
Perhaps the greatest challenge lies in maintaining momentum after the initial rollout phase:
- Regularly refresh safety messaging to prevent "safety fatigue" and keep content engaging
- Use a variety of communication channels (SMS, digital signage, in-person meetings) to reach all workers
- Develop a recognition program that acknowledges and rewards ongoing safety compliance
- Share success stories and improvement metrics to demonstrate the impact of safety efforts
- Conduct periodic "safety stand-downs" to address emerging issues and reinvigorate commitment
To maintain momentum, consistency makes the difference. Regular safety audits combined with meaningful feedback loops create a culture where safety becomes ingrained in daily operations rather than viewed as a separate initiative.
Addressing these common challenges head-on with practical solutions within your safety improvement plan builds a safety program that delivers sustainable results for your non-desk workforce.
Safeguarding Your Workforce: The Next Step Forward
Effective safety improvement plans establish safety as a core value embraced throughout the organization. For non-desk workers, communication presents a persistent challenge that traditional methods often fail to address.
Yourco's SMS-based platform instantly connects with your entire frontline workforce, delivering safety updates and alerts with a 98% read rate. Unlike emails, text messages ensure safety communications are seen in real-time, potentially preventing accidents instead of responding after incidents occur.
But Yourco is more than just a messaging tool—it’s a centralized documentation and communication hub for safety. Employees can snap a picture of an injury, property damage, or unsafe condition and send it—along with a brief description—directly to their company’s dedicated Yourco number. That message is instantly time-stamped and stored as part of the organization’s internal incident record. This dramatically reduces the delay between incidents and reports—no more waiting until the end of the shift or relying on memory. In case of a dispute, companies can demonstrate exactly what happened and when. HR or safety managers can follow up to gather further details, ensuring nothing slips through the cracks.
In addition to real-time alerts and reporting, Yourco helps you distribute training materials, conduct safety surveys, coordinate emergency response, and document compliance—all through a secure, familiar channel: text messaging. No apps, downloads, or logins required.
Whether you're managing a single job site or a decentralized workforce across multiple regions, Yourco helps you maintain a continuous feedback loop, foster accountability, and protect your teams in the moments that matter most.
Try Yourco for free today or schedule a demo and see the difference the right workplace communication solution can make in keeping your non-desk workforce safe, connected, and empowered.